How to Implement Reliability Centered Maintenance (RCM)
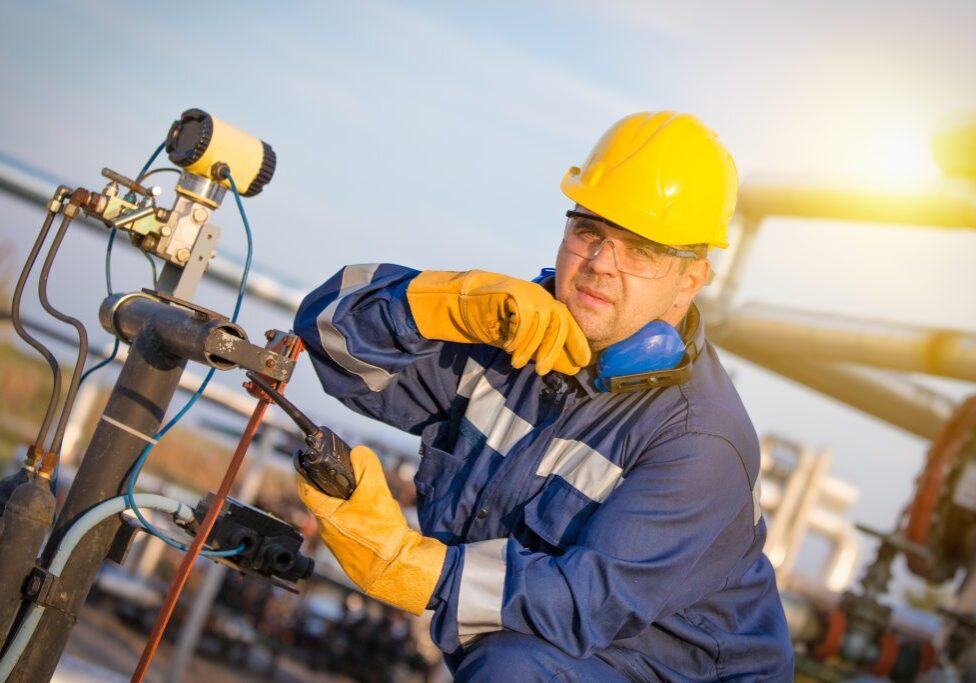
We’ve previously written about Proactive Versus Reactive Maintenance and decided to build on that with a practice called Reliability Centered Maintenance. We will show you the steps and benefits to implementing it in your organization.
What is Reliability Centered Maintenance (RCM)?
RCM is the practice of focusing on the reliability of your equipment rather than standard scheduling and budgeting practices. It is used to determine what tasks should be performed to ensure that physical assets continue to operate as desired for the foreseeable future. Unique maintenance schedules are developed for each critical asset within an organization or facility when initializing RCM.
Steps to Determine Reliability Centered Maintenance
Reliability centered maintenance identifies the basic requirements your program must meet. You should analyze the following data on each critical asset as part of the process.
- What is the equipment’s main function and what standards of performance it should meet?
- How can the equipment fail to provide the required functions?
- Identify the events that may each failure along with the consequences of each scenario.
- How does each failure matter in lost time, cost, etc?
- Which tasks can be performed to prevent the failures or diminish their consequences?
- Determine an alternative if a suitable preventive task cannot be developed via contractor, third party, manufacturer, or other.
Steps to Implement Reliability Centered Maintenance
The above are used to determine the three main hurdles in RCM: decision, analysis, and act. You must decide on a course of action, analyze its benefits and drawbacks, and make a decision based on this information.
Decision – Make decisions based on your desired outcomes and be sure to include as many relevant opinions as possible. This includes discussing these outcomes with equipment operators, maintenance employees, project managers, subject matter experts, and executive leadership. You may also need to examine current equipment to see if it can benefit from RCM or needs to be replaced.
Analysis – With this data, you can move onto one of the most essential parts of analysis: functional failure. It is the inability of your equipment or system to meet the previously established standards of performance. As an example, a total functional failure would be a motor that doesn’t rotate due to lack of lubrication. A partial failure is a motor that underperforms due to lack of lubrication.
Act – Use all your data and analysis to determine courses of action for each possible scenario. This includes setting proactive maintenance tasks to prevent equipment failure. It can be usage or calendar based, whichever is best to detect and prevent a failure before it begins.
Houston Dynamic Supply Component Maintenance & Repairs
We are one of the leading equipment maintenance and repair shops in the Gulf Coast region. Our capabilities include hydraulic testing of pumps to expert evaluation of equipment to determine what repairs or upgrades will deliver the best performance. Call us today to discuss your equipment maintenance needs.
Share this post: