Proactive Versus Reactive Maintenance
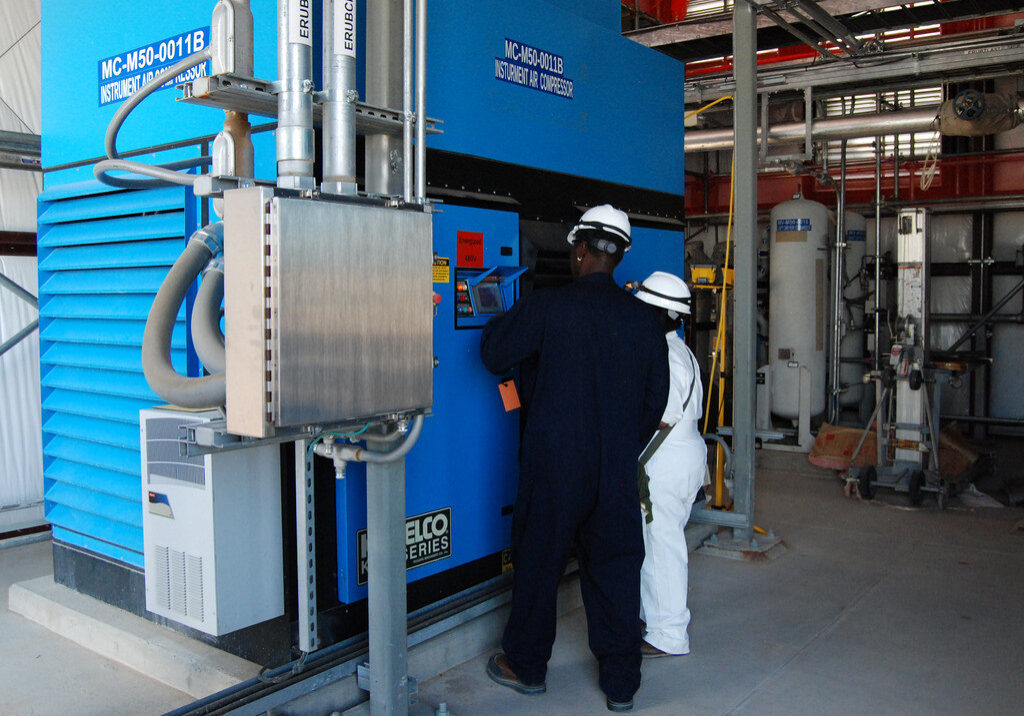
Many organizations are realizing the benefits of embracing a proactive maintenance approach. Others still rely heavily on a reactive maintenance strategy, or wait for problems to arise before dealing with them. This ultimately leads to reduced asset insight, improper planning, time delays, unexpected costs, and a resulting inefficient maintenance plan. It is important to find the right balance of proactive and reactive maintenance to increase the reliability and performance of your operation while simultaneously reducing operating costs. Numbers vary by industry, but studies have shown that in general, the ideal balance is 75% proactive to 25% reactive maintenance.
Proactive vs Reactive Maintenance Cost
Reactive maintenance deals with issues as they arise, which ends up costing less in the present as the strategy does not require you to invest in future plant maintenance. However, owners will inevitably spend far more in money and lost resources in the long run. The Marshall Institute reports that owners who practice reactive maintenance can spend two to five times as much as those who implement proactive maintenance.
Proactive vs Reactive Maintenance by the Numbers
Consider a study conducted by Plant Engineering a few years ago. They surveyed engineers and maintenance professionals in order to get an overview of maintenance strategies in the United States. Thirty-one percent of respondents reported they implemented proactive maintenance programs with the primary purpose of reducing unscheduled downtime. Less than 50% reported they applied some form of proactive maintenance program. Unfortunately, 57% of all respondents admitted to still conducting reactive procedures most of the time, and that it came with disadvantages in regard to cost, safety, downtime, and energy usage.
Some of the more interesting numbers included:
- Approximately 45% of those who used predictive maintenance reported energy savings as opposed to approximately 5% of those who used a reactive strategy.
- Approximately 75% of those who used predictive maintenance reported decreased downtime as opposed to approximately 25% of those who used a reactive strategy.
- Approximately 55% of those who used predictive maintenance found the strategy to be cost effective overall as opposed to approximately 25% of those who used a reactive strategy.
- Approximately 55% of those who used predictive maintenance reported improved safety as opposed to approximately 5% of those who used a reactive strategy.
Other Benefits of Proactive Maintenance
Proactive maintenance is also referred to as preventive maintenance or scheduled maintenance. It is a precautionary management style where maintenance and inspections are regularly scheduled and carried out. The goal is to ensure equipment is operating within parameters to minimize or eliminate breakdowns, as well as trade repair costs for less costly maintenance procedures.
Other benefits:
- Extending the operating life of equipment.
- Optimizing equipment efficiency.
- Reducing energy costs.
- Increasing operating transparency and accountability.
- Fewer machine breakdowns and outages.
- Better planning for spare parts and labor.
- Decreasing the necessary amount of large and small-scale repairs.
- Improved compliance with health and safety requirements.
- Better adherence to production schedules.
- Improved customer service through continuous and efficient overall production.
HDS has a fully staffed service center with experienced personnel, dedicated to quality and trained in the most current rotating equipment maintenance, inspection, and repair techniques to help your operation. Call us today to discuss your maintenance plan and how we can partner with you to proactively meet your needs.
Share this post: