The Importance of Oil Level Control in Equipment Performance
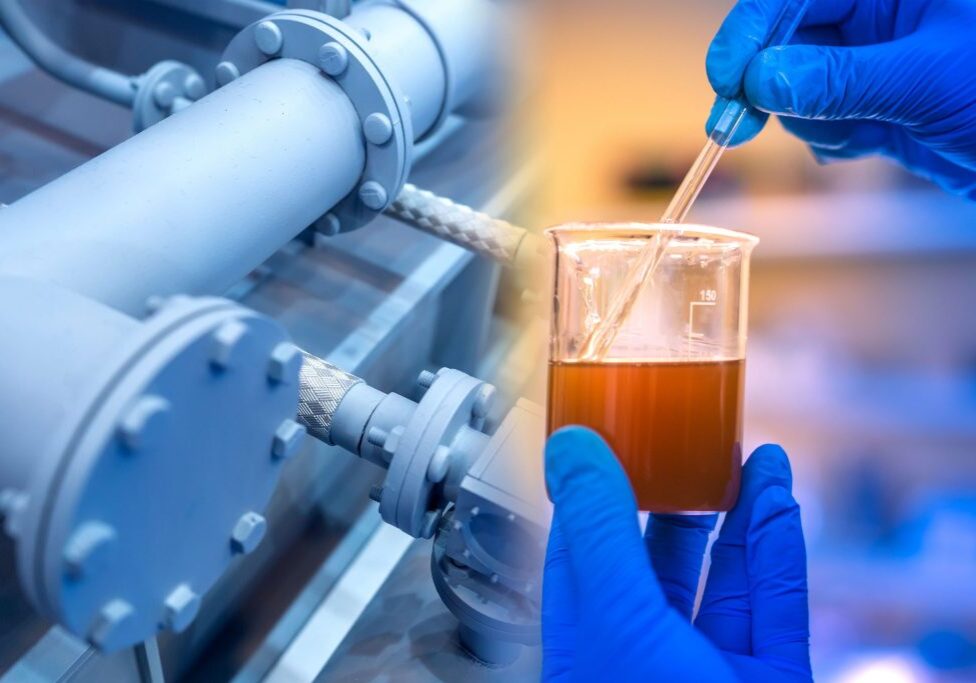
Precision lubrication means utilizing various data points and expert advice to choose the best lubricant, frequency, method, and volume needed to optimize performance and extend the lifespan of critical equipment. This is the goal of any maintenance program, and data is constantly changing. One thing that should be on your mind is the importance of oil level control in equipment performance.
Proper Lubricant Level
Many experts find themselves confused by the “proper lubricant level” and why a specific amount is considered proper. In short, the proper level is simply the level that allows for optimal equipment performance for the intended process. There are two main factors to consider when determining the correct amount of oil: equipment performance and process requirements:
- Size of equipment – Size plays a key role in deciding how much lubricant a component should receive, whether it is a gearbox, motor, bearing, pump, or hydraulic system. Some situations call for more lubricant than generally allowed, such as larger bearings in greased applications.
- Equipment speed – Lubricant levels must be adjusted to the speed used by the equipment in your specific process, especially in greased applications. For example, a slow-moving greased bearing will most likely need to have grease packed into the bearing at a higher volume during installation. You may need less lubricant than originally thought here, depending on load, viscosity, etc.
Lubrication Methods
There are several methods used so you must choose the lubrication method best suited for your equipment:
- Oil Splash: Splash is the most common form of lubrication. Parts may be in direct contact with lubricant, or you may use oil rings and flingers to apply. Splash lubrication is good for regulating temperature and is most effective when oil is filtered and replenished on a consistent basis. Oil rings or flingers take the oil and transfer it over the necessary parts. This method requires you closely monitor the levels. Too much and it the tool will submerge and not adequately disperse the oil. Too little and there will not be enough to lubricate the necessary parts.
- Oil Misting: This method uses compressed gas to disperse oil. Low pressure systems distribute this oil at multiple areas for optimal lubrication. This method is good for keeping equipment lubricated while decreasing any temperature fluctuations. It is the best lubrication method on the market today for many types of rotating equipment.
- Grease: This method is used for many machine elements but can experience temperature limitations. As a pro, grease has sealing properties and can reduce leakage and contaminants. However, it does not dissipate heat as well as oil mist and oil splash systems. Grease may also take longer during start-up for adequate lubrication to occur.
Post Lubricant Checks
Did you know that approximately 40% of machine failures derive from incorrect applications and selection of lubricants? Once you have determined the correct type, level, etc. you must test the equipment to ensure your choice was correct. This includes testing your lubricant after application for correct formulation, amount of lubricant, and assessing the lubricant performance.
Houston Dynamic Supply Can Help Determine the Proper Oil Level for Your Equipment
Our team of experts can help you determine the best way to lubricate your rotating equipment. We can also repair, refurbish or replace your faulty equipment. HDS specializes in all types of rotating equipment and lubrication, such as centrifuges, compressors, turbines, blowers and pumps. Our industry-leading Gulf Coast facility has everything you need to keep your equipment running at its best.
Share this post: