Strategies to Reduce Cavitation in Centrifugal Pumps
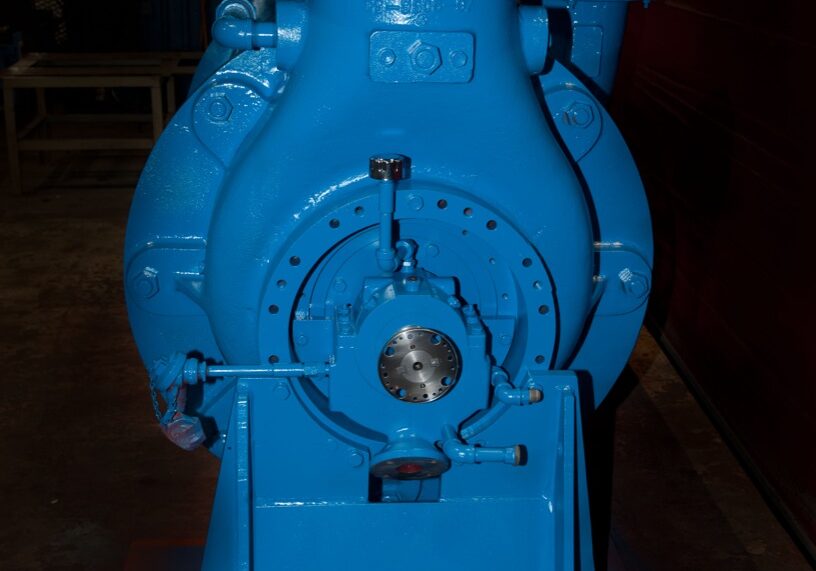
The team at Houston Dynamic Supply have seen all sorts of issues with rotating equipment, including centrifugal pumps. One of the most common and devastating is cavitation. This happens when vapor bubbles form in low-pressure pockets and implode when entering into higher pressure areas. It leads to all sorts of damage on pump internals and can result in erosion and corrosion.
What Causes Pump Cavitation in Centrifugal Pumps?
Many operating conditions can lead to cavitation. For example, a clogged strainer or filter can restrict the pump’s flow and cause cavitation.
Other common causes of cavitation include:
- Blockage in the pipe.
- Faulty inlet hose.
- Incorrect fluid viscosity.
- Pump running on wrong curve.
- Wrong NPSH requirements.
- Other poor pump designs.
How to Diagnose Pump Cavitation?
You may be able to determine on your own, if a pump has cavitation. One of the main indicators is that the pump’s performance will be off and noted by reduced pressure or flow. You may also notice excessive vibration or noise in the pump that can lead to failures in the seals and bearings. Since the pump is working harder, you may also notice higher power consumption.
Unfortunately, pump cavitation cannot always be detected by these traditional signs. On many occasions, cavitation occurs on the internal level first. It can damage seals, bearings, o-rings, the impeller, pump housing, and other components. You may even see leaks in the pump before it displays any of the above symptoms.
How to Prevent Pump Cavitation
Centrifugal pumps have high flow rates and outputs that notoriously lead to cavitation. Be sure a centrifugal pump is right for your application and process before installing if cavitation is a major concern. You may also prevent cavitation by doing any or all of the following:
- Always use the recommended amount of liquid.
- Keep the inlet hose as short as possible.
- Use the recommended diameter for your inlet hose.
- When possible, use flexible inlet hoses with internal springs.
- Check and clean the inlet hose for any restrictions, blockage, too many elbows, and the proper fittings.
- Decrease any head loss from fittings. You may do so by reducing the number of fittings on the suction lines and using specialized fittings.
- Inspect and clean filters and strainers on a regular basis or avoid whenever possible.
- Install the tank reservoir over the pump so it can be fed by gravity.
- When necessary, reduce the temperature of the pump fluid to lower vapor pressure.
In short, you are avoiding cavitation by ensuring the centrifugal pump’s pressure is kept above the liquid’s vapor pressure. Finally, our best strategy to reduce centrifugal pump cavitation is to work with experienced professionals to ensure the proper selection, use, repairs, and placement of the pumps for your desired outcome(s).
The team at Houston Dynamic Supply team has years of experience helping all sorts of organizations diagnose, prevent, and repair any damage caused by pump cavitation. Contact us to speak with our experts about how we can help you prevent cavitation in your centrifugal pumps, or upgrade/retrofit your pump to better prevent cavitation.
Share this post: