Extending Pump Life After a Rebuild: Best Practices for Maximum ROI
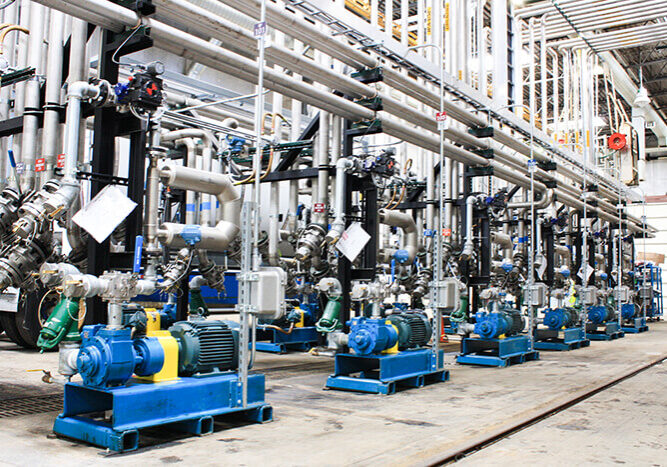
Industrial pumps are critical assets in most processing facilities, and their performance has a direct impact on reliability, safety, and operational costs. At Houston Dynamic Service, Inc. (HDS), we specialize in precision pump rebuilds that restore your equipment to like-new condition. However, even the most expertly rebuilt pump can fail prematurely if it’s not maintained properly. This article outlines essential strategies for maximizing the service life and return on investment (ROI) of your pump after the rebuild.
Why Rebuild Instead of Replace?
Rebuilding is often the smarter choice when facing pump wear or failure. It can reduce lead time by weeks or even months compared to ordering a new unit—especially for OEMs with limited availability. Additionally, a professional rebuild typically costs 40–70% less than a new replacement, depending on the scope of work.
At HDS, our rebuilds follow rigorous OEM standards and include full disassembly, non-destructive testing, rebalancing, and the installation of upgraded materials where applicable. But what happens after the rebuild is just as critical.
Protecting Bearings: How to Prevent Brinelling
One of the most common causes of post-rebuild pump failure is brinelling—the formation of indentations on bearing surfaces due to metal-to-metal contact. This can occur during storage or startup and typically results from improper support, impact, or inadequate lubrication. There are two types to watch for:
– True brinelling: Caused by heavy static loads during handling or transport.
– False brinelling: Results from micro-vibrations over time, especially during storage without rotation.
Both can significantly reduce bearing life, create elevated noise levels, and increase torque requirements during operation.
HDS Recommendation:
Use assembly lubricants specifically designed for rolling-element bearings. These lubricants:
– Offer superior anti-wear properties,
– Reduce operating temperatures,
– Displace moisture, and
– Provide rust protection during downtime.
Our technicians at HDS recommend high-performance synthetic or semi-synthetic lubricants that meet or exceed OEM specifications, particularly in critical applications.
Corrosion Protection and Vapor Phase Inhibitors (VPIs)
Even a small amount of moisture intrusion can lead to oxidation, corrosion pitting, and premature failure. For long-term storage or standby pumps, enhanced lubricants with vapor-phase corrosion inhibitors (VCIs) are highly effective. These formulations protect both contact and non-contact metal surfaces inside sealed housings.
Technical Tips:
– Ensure magnetic contact seals are used to completely seal the bearing housing.
– Remove breathers and plug all ports when storing pumps to eliminate air exchange.
– Test seal integrity using a balloon test: connect a balloon to a breather port; if it deflates, your seal is compromised.
Mineral oils typically protect bearings for 6 months, while synthetic lubricants with VCIs can offer protection for up to 2 years.
If your pump is already filled with lubricant, consult the manufacturer before adding a VCI concentrate to ensure compatibility.
Storage Matters: Protecting Pumps During Downtime
Improper storage is one of the leading causes of failure in rebuilt pumps that never return to service. The effects of uncontrolled humidity, dust, UV exposure, and temperature swings can cause seal degradation, shaft misalignment, and component fatigue—even before the pump is turned on.
Indoor vs. Outdoor Storage:
– Indoor Storage: Maintain a climate-controlled environment with low humidity. Use desiccant breathers or vapor corrosion inhibitors.
– Outdoor Storage: Cover volutes and shafts with protective coatings and weatherproof wraps. Use desiccant packs or VCI bags and inspect seals regularly.
If storing pumps filled with oil, be mindful that oil viscosity changes with temperature. This can cause inadequate lubrication during cold starts or sludge formation during high-heat exposure.
HDS Tip:
Manually rotate pump shafts every 6–8 weeks to prevent false brinelling and redistribute lubricant. This also provides an opportunity to check for developing issues.
Final Thought: Maintenance is Your ROI Multiplier
A rebuilt pump is only as reliable as the maintenance and storage practices that follow. Preventative maintenance is always more cost-effective than unexpected shutdowns and reactive repairs. Following the manufacturer’s service intervals, using premium lubricants, and ensuring proper storage conditions can increase pump lifespan by 25% or more.
At Houston Dynamic Service, we go beyond the rebuild. Our experts provide onsite evaluations, customized maintenance schedules, and lubricant selection guidance tailored to your specific application. We also offer rotating equipment storage solutions for clients with surplus inventory or extended maintenance cycles.
Need Help Extending the Life of Your Rebuilt Pump?
Contact Houston Dynamic Service, Inc. for:
– Precision pump rebuilds
– Lubricant and corrosion protection guidance,
– Turnkey maintenance services.
📞 Call us today or visit houstondynamic.com to learn how we can help protect your investment and maximize uptime.
Share this post: