Equipment Series – Fans and Blowers
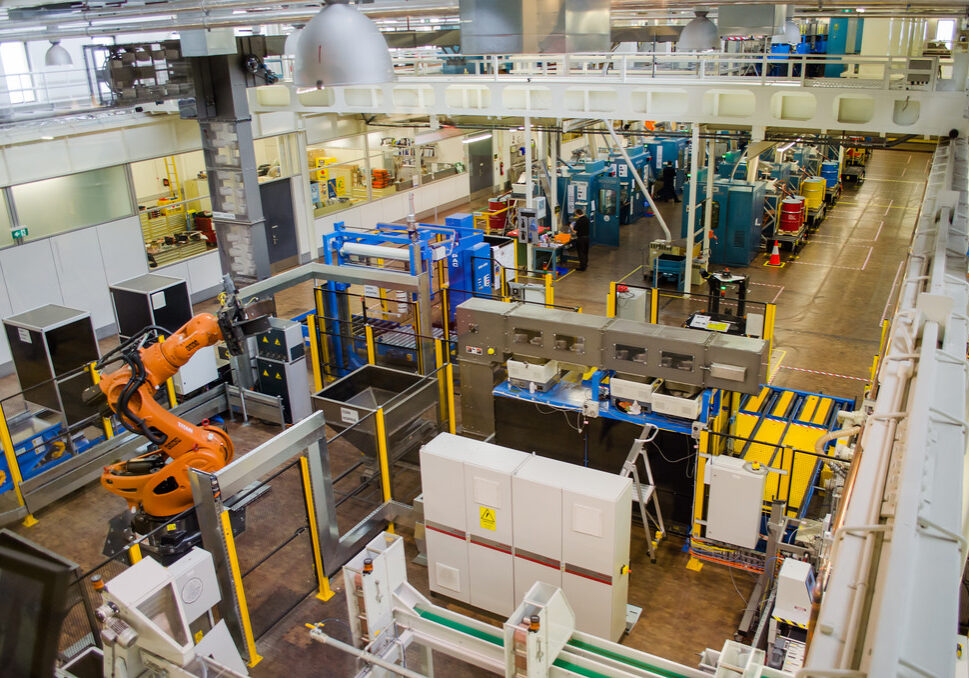
Continuing our Equipment Series, we turn to fans and blowers. These pieces of equipment provide air for ventilation and industrial process requirements. They often use a rotating shaft to transmit energy in order to move the air. Fans and blowers are designed to generate pressure to move air or gas against resistance such as ducts, dampers, or other fan system components.
Difference Between Fans and Blowers
Fans and blowers are differentiated by the method and pressure they use to move air. The American Society of Mechanical Engineers has designated a specific ratio of discharge pressure over suction pressure. In short, the ratio of pressure in fans is under 1.1. Blowers have a pressure ration of 1.1 to 1.2. Anything higher than 1.2 is considered a compressor.
Types of Fans and Blowers
Each type of equipment has several models with its own applications. Some of the most common are:
- Axial fan – Air enters and leaves the equipment with no change in direction. They offer a peak efficiency of as low as 45 in a propeller fan and up to 85 in a vanaxial fan.
- Centrifugal fan – The airflow changes direction when it enters and again when it exits. These fans offer a peak efficiency of as low as 60 in a forward curved fan and up to 83 in an airfoil fan.
- Centrifugal blower – Its impeller is generally gear-driven and can rotate as fast as 15,000 rpm. Centrifugal blowers may operate against pressures of 0.35 to 0.70 kg/cm2.
- Positive-displacement blower – They use rotors to collect air and push it with a constant volume, regardless of the system’s pressure. These blowers turn slower at 3,600 rpm and can produce pressures up to up to 1.25 kg/cm2.
Each piece of equipment comes with its own pro’s and con’s. For example, positive-displacement blowers are great for applications that are prone to clogging. This is because they typically produce enough pressure to blow out clogged materials.
Another example is the axial propeller fan. It generally runs at lower speeds and moderate temperatures. Small changes in static pressure can cause large changes in airflow, but the fans can handle large volumes of air at low pressure. Propeller fans are often used indoors because their efficiency in outdoor applications may drop to 50% or less
Fans and Blower Issues
A malfunction in a fan or blower can wreak havoc throughout the entire system, as well as violate certain safety protocols. Below are some issues fans and blowers can experience.
- Excessive noise/vibration – The issue may not necessarily collapse the system but can cause damage to equipment and also comes with higher energy costs. Fan blades that are not balanced or loose components commonly cause the issue. Noise or vibration should be addressed and corrected as quickly as possible to increase the life of the equipment.
- Shaft damage or misalignment – The issue is far more serious than the above. If the blades of your equipment are pointed in the wrong direction or you notice wobbling in the unit, you may have a damaged or misaligned shaft. They can be expensive to repair but much cheaper than an unexpected shutdown.
- Damaged components – Fans and blowers can have any number of components from bearings to housing and much more. When these parts become damaged, they cause unsafe and inefficient operations. Having the units inspected and repaired is the best way to combat any further damage.
- Worn out filters / separators – The manufacturer specifies when to check and change filters and related parts, but each operation is different. These parts can corrode erode at much different levels than intended depending on application. The unit may even need to be disassembled in order to inspect and replace the parts.
Conclusion on Fans and Blowers
At Houston Dynamic Service, we have extensive knowledge on how to rebalance, machine or replace parts on all types of fans and blowers. To learn more, contact us to discuss how we can keep your system running at its best!
Share this post: