4 Maintenance Tips to Extend Equipment Life and ROI
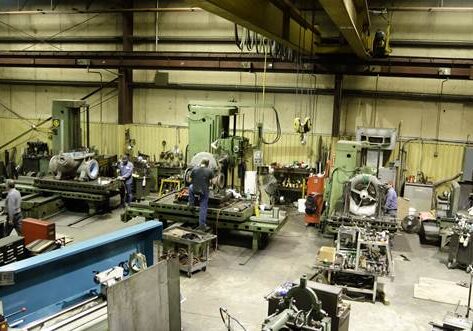
Heavy machinery, especially in oil and gas, mining, farming, or other industrial applications, requires regular maintenance to ensure they continue working reliably. When large machinery is poorly maintained, it not only runs inefficiently, but is also more likely to breakdown and cost you thousands – not to mention that faulty equipment can pose a serious safety hazard. To prevent premature breakdowns and lost revenue, here are 4 tips for maintaining your large machinery.
-
Develop a Comprehensive Preventative Maintenance Plan
Minimize potential downtime from equipment failure that could have been avoided by implementing a broad maintenance plan. Your owner’s manual no doubt has lots of tips for maintenance including what needs to be done and when. These plans are important for detecting problems before they become major issues. Your plan should be designed to ensure operations reach their full potential without the risk of equipment damage by anticipating what wear and tear to certain components looks like. The plan should include both regular maintenance and preventative maintenance beyond the usual changing of filters and lubrication. Think of it as an all-inclusive strategy to keep asset management at its best-case scenario.
The goal of these plans should include but are not limited to the following:
- Elimination of unexpected breakdowns.
- Lower risk of system or component replacement.
- Longer lifespan in equipment.
- Better resale value should the equipment be sold.
- Improved parts inventory management.
- Enhanced equipment reliability.
-
Train Your Operators
Your equipment is likely to have multiple operators. A key part of extending your equipment’s life is the proper training and management of those who operate the equipment. Operator training is usually done as soon as equipment is purchased, but personnel comes and goes. Even the most skilled operators can lose their edge as time goes, making the work repetitious. Feel free to revise your operator manual as needed for your specific applications. You may also simplify and shorten the language to better transfer proper operations procedures to your readers. It is also recommended to draft a best practices for operations as applied to other facilities, locations, etc.
-
Identify Common Causes of System Breakdown
Your plant may spend hundreds of thousands of dollars by not identifying potential causes of issues before they arise. Machinery failure can generally be broken down into three categories:
- Gradual Failure – This type of failure can be prevented almost entirely by performing routine inspections and maintenance to check for and prevent extreme wear and tear.
- Intermittent Failure – This is a failure that does not happen often and is more difficult to identify. It is usually a failure of equipment that goes “in and out.” Like the old adage goes: the car never rattles when you take it to the mechanic. However, intermittent failure can cause frustrating, repeated downtime that may have been avoided with a maintenance plan. It is important to identify and fix the cause of an intermittent failure before it leads to:
- Sudden Failure – This is when your equipment breaks down without warning. The cause of the problem only presents itself once the equipment is inoperable. The only solution to sudden failure is to identify and fix the problem as soon as possible.
-
Test and Lubricate Frequently
Large machinery is often scheduled for inspections and tests to prevent any type of failure described above. This includes the addition of the proper lubricants to reduce friction around moving parts. Adhering to a good lubrication schedule helps to extend the life of large equipment and their parts, just as regular oil changes help extend the life of your car. You should look for signs of excess oil, grease build up, leaks, and more during lubrication. The right lubricant should always be used, as different machinery uses different lubricants.
HDS has a fully staffed service center with experienced personnel, dedicated to quality and trained in the most current rotating equipment maintenance, inspection, and repair techniques. Call us today if you want to discuss your equipment maintenance needs!
Share this post: