4 Steps to Set Up a Proactive Maintenance Plan
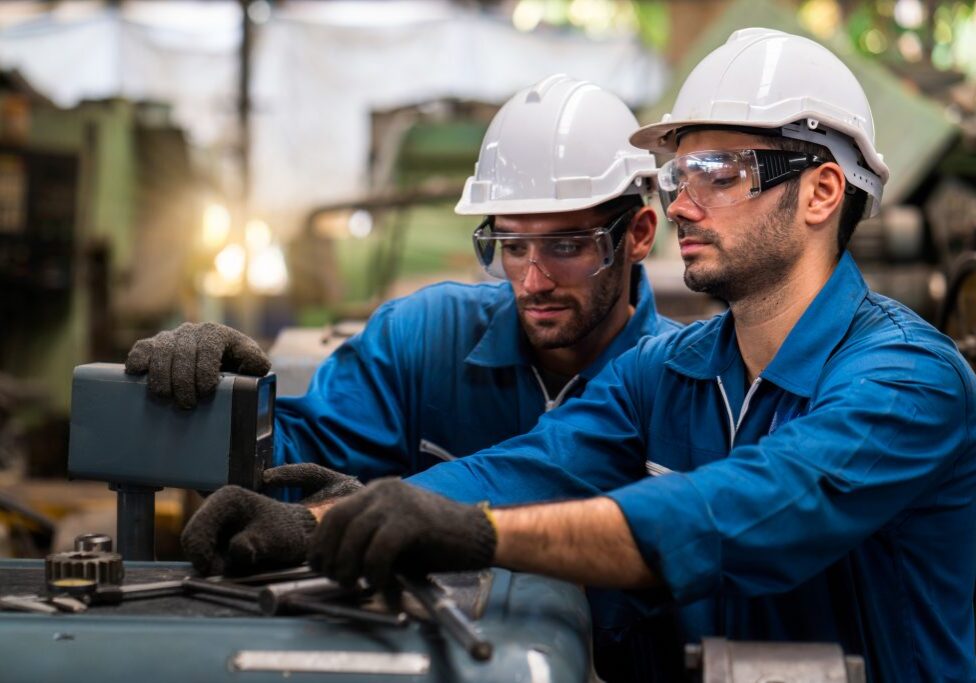
We’ve previously written about Proactive vs Reactive Maintenance – but there is more to say on the topic. It is one thing to know what proactive maintenance is. It is another thing entirely to implement it correctly in your organization. Here are four crucial steps to implement.
- Create a RAMS Team
Reliability, availability, maintainability, and safety are the focus of this team. It should be comprised of highly trained engineers and techs. They must be able to properly utilize your asset management system. Tasks they will asked to perform include root cause analysis, failure analysis, and failure modes and effects analysis, as well as other related activities.
- Begin with Proper Training
Maintenance techs and engineers must be on board with the change to proactive maintenance. They should be trained and committed to implementing the proactive mindset. This includes workflow changes as well as learning new techniques and the operation of new tools. One of the best ways to accomplish this is to involve them in all stages of the process. Make sure to show them how this will make their daily work easier.
- Use a CMMS
You may already have a Computerized Maintenance Management System. It should allow you to centralize and streamline all of your maintenance operations. This includes managing schedules, checklists, work orders, inventory for spare parts, and other maintenance related work. If you don’t have one, a CMMS allows proactive maintenance to be far easier. In addition, the accuracy and timely information it provides can actually help prevent previously unforeseen breakdowns. Some CMMS platforms actually allow you to perform condition-based monitoring wherein you receive alerts if a certain piece of equipment or process performs outside established parameters. They can use remote monitor devices to feed data to you and trigger pre-defined actions. For example, you could program a piece of equipment to power off if its operating temperature exceeds the standard. Finally, a CMMS can generate a detailed, up to the minute report on all your monitored processes.
- Be Prepared to Invest
Unfortunately, doing the above does take funds. The good news is you can make it all back from streamlining workflow and data generation, avoiding premature breakdowns, helping prevent shutdowns, and extending the life of equipment. In fact, you may be able to calculate the cost of these past events and compare them to the costs of proactive maintenance implementation to see how long it will take to recoup the costs.
In addition, you need to have enough tools and personnel to carry out designated proactive maintenance tasks. You may encounter delays in which technicians don’t have the time to execute tasks without enough manpower. You may also experience delays if you have to wait for tools or parts to perform these assigned tasks.
Houston Dynamic Supply Root Cause Analysis
HDS have over 30 years of experience repairing and upgrading rotating equipment used in many industrial applications. We can assist in a proactive maintenance plan by diagnosing the cause of many issues, along with their solutions. We can also help test equipment that appears to be in good working condition to verify. HDS works with all types of rotating equipment and offers OEM capabilities. Our experts provide precision machining, rebuilds, and repairs. Contact us today to learn more.
Share this post: