Top Tips for Improving Pump Reliability
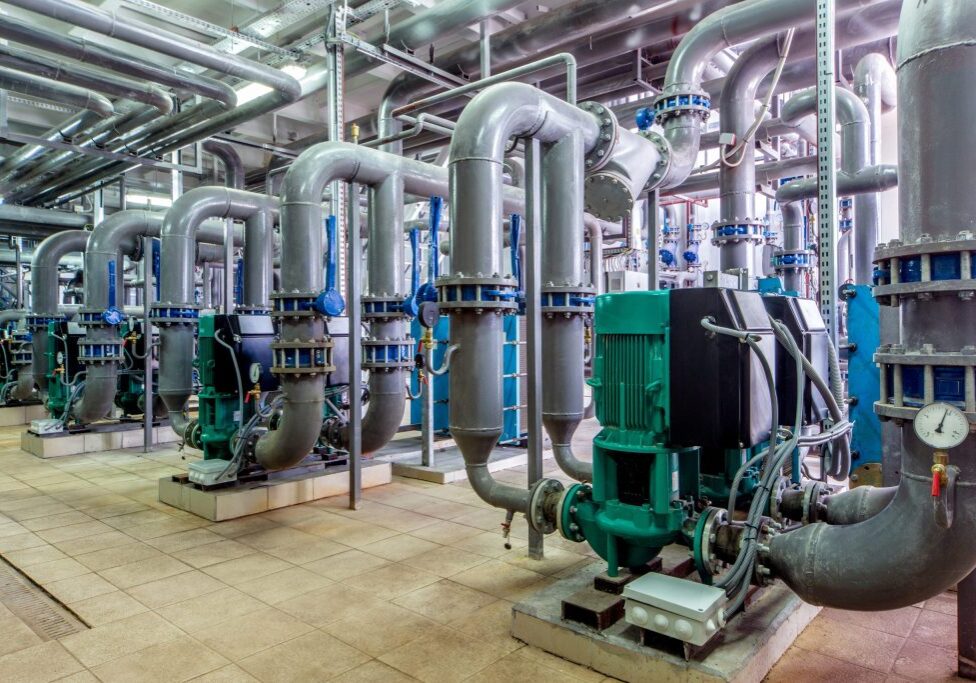
A large section of our industry can regularly use anywhere between a few hundred to several thousand pumps in their facilities. These pumps are connected to many other pieces of essential rotating equipment such as compressors, fans, blowers, turbines, and more. These organizations may have a yearly average budget of millions of dollars set aside for maintenance and need to make the most of it. As a result, improving pump reliability is more important than ever to reduce usage costs while extending the lifespan of the equipment. Our top tips for improving pump reliability are focused on the least effort with the maximum pay off.
-
Evaluate and Update Current Pump Reliability Maintenance
Your current pump maintenance may be done either through a combination of condition based monitoring and manual rounds with the goal of preventing failures. Unfortunately, manual monitoring is usually costly and full of human error. In addition, manual reviews cannot generally determine if a pump or system is performing at optimal efficiency. Fortunately, better options are available.
-
Advanced Health Monitoring
New technology is constantly developing to allow users, operators, and even owners to get an overview of their pump systems’ health at a glance. It is essential to purchase, install, and upgrade any current system in order to get regular, real time hard data. This allows you to make informed decisions on maintenance and other considerations. In fact, today’s technology allows you to get vital information on:
- Pumps that may lead to a failure, fire, or other incident.
- Pumps that may lead to a disturbance in the process, slow down, or even shutdown.
- A pump that does not have a spare or backup.
- Repeat failures in pumps and systems.
- Vital data on energy usage, output, and spikes in either.
- Vital data on pumps that were previously considered “not vital” enough to invest in advanced health monitoring.
-
Pumps Should be Right-Sized
Unfortunately, we’ve seen many systems that use pumps that are too big or too small for their process. An incorrectly sized pump will have inconsistent liquid flow and excessive forces on the impeller. These pumps can operate at a reduced or increased flow rate, which results in pressure imbalance, shaft deflection, heavy loads on bearings and seals, increased heat and vibration, and other conditions that will affect your process, reduce the operating life of the pump itself, and can cause premature failure.
-
Consider Surface Coatings on Pumps
Most common pump applications can benefit from inexpensive yet effective coating upgrades. They are one of the best ways to improve performance while increasing the mean time between failure. Coatings may be designed to reduce friction, erosion, and corrosion. They can be applied to the impeller’s rough surfaces as well as the volute to offer protection and increase efficiency. These coatings can also be used on bearing housings and other external pump surfaces for certain applications
Houston Dynamic Supply Can Reduce Your Pump’s Total Cost of Ownership With Design Enhancements
Our team has the expertise to reduce the cost of ownership in all rotating equipment such as centrifuges, turbines, compressors, fans, blowers, and of course: pumps. We can help you determine the best course of action for upgrading and repairing your system versus the costs of repairing or replacing. Our Gulf Coast facility is state of the art and houses all the equipment and personnel you need to make the best decision for your operation.
Share this post: