Top Six Pump Vibration Problems
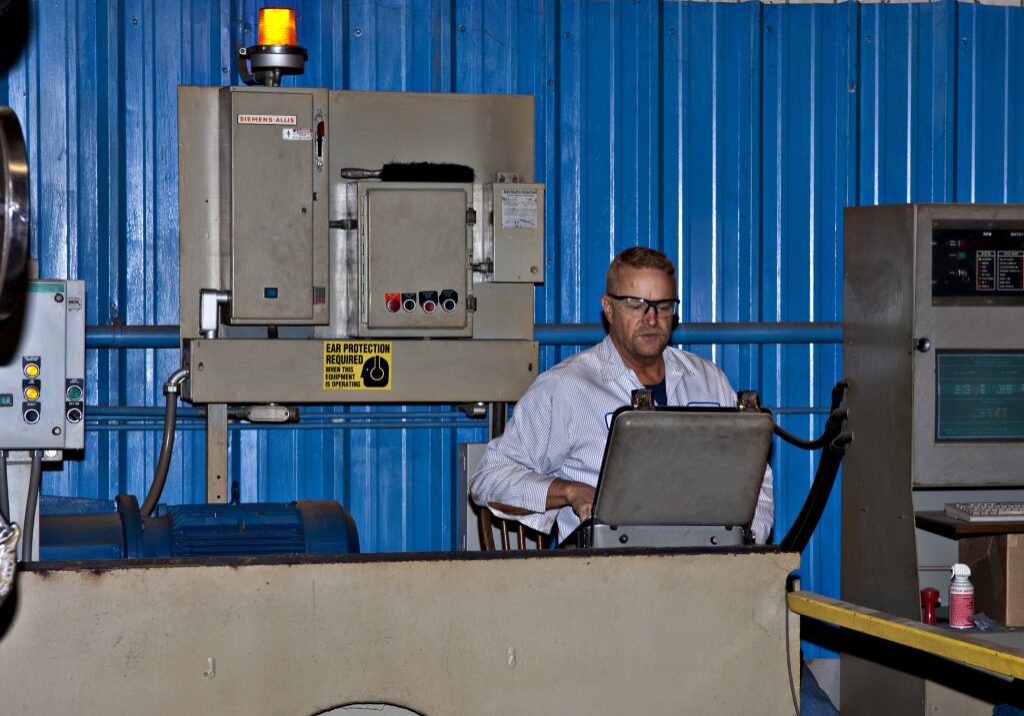
Houston Dynamic Service’s technicians are dedicated to quality and trained in the latest rotating equipment repair techniques. Given our combined years of experience, we have seen the range of things that can go wrong in a large variety of pumps. We would like to share some of the knowledge that is gained through that experience.
A high percentage of the pumps brought to us for repair are experiencing a vibration problem. There are six main causes of pump vibration problems and any one could take a pump out of service for unplanned and expensive repairs. Read on for tips to help you determine whether your pump’s poor performance is due to one of these vibration problems.
#1: Pump Cavitation
Pump cavitation is a symptom of insufficient net positive suction head. It occurs when the absolute pressure of the liquid at the impeller inlet approaches the liquid vapor pressure, causing pockets to form and collapse as they pass through the impeller.
You can often identify pump cavitation by the sound of the pump – like rocks are rumbling in the pump or distinctive popping. Beyond excess noise, higher energy usage and damage to the pump may be observed.
You can prevent cavitation by:
- Checking the filters and strainers for cleanliness
- Using a pressure gauge or flowmeter to reference the pump’s curve
- Reevaluate pump design if the pumped media path is not ideal
#2: Bent Pump Shaft
A pump with a bent shaft can cause high axial vibration with axial phase differences that tend towards 180° on the same rotor. A dominant vibration normally takes place at 1X RPM if the bend is near the shaft center. It can occur at 2X RPM if it is bent near the coupling. Bent pump shafts are more likely to happen at or near the coupling.
You can identify a bent pump shaft by using dial indicators.
#3: Pump Flow Pulsation
This condition develops when a pump is operating near its shut-off head. Pressure gauges on the pump’s discharge piping will fluctuate. If the pump uses a discharge swing check valve, the counter-weight and valve arm will move to indicate unstable flow.
One of the major causes of pulsation is the lack of proper feed. The pumped media must maintain contact with the face of the plunger as the plunger is retracted and the pump is full. If not, the plunger moves forward and impacts the fluid causing unwanted pulsation. You can help prevent pump flow pulsation by using a suction stabilizer to keep the fluid in constant contact with the plunger.
Other causes of pump flow pulsation include:
Improper spring rates
- Leaking valves
- Multiple pumps on a common header
- Piping designs that restrict flow
- Worn packing
#4: Pump Impeller Imbalance
Pumps can at times seem as if they are misaligned, have bad bearings, or are overheating, but the cause is often an imbalance in the pump assembly or another component. Imbalance also causes vibration and heat buildup. Impellers should be precision balanced, which has a huge impact on the life of the pump bearings.
If the pump’s impeller is center-hung, force imbalance is more common than couple imbalance. In this case, the highest vibration will most likely be in the radial direction with the highest amplitude at pump operating speed (1X RPM). Center-hung impellers use balanced axial forces on the inboard and outboard bearings. Extensive axial vibration in impellers is indicative of an obstruction by a foreign object.
The dangers of pump impeller imbalance include:
- Shaft deflection – bent shaft or uncontrolled resonance that can result in deflection and damage the entire system
- Bearing failure
- Excessive vibration that damages the pump or system
- Failure of the mechanical seals or packing
- Seizing of the pump
#5: Pump Bearing Issues
One of the leading causes of pump vibration problems is bearing failure. This is because an estimated 10% to 30% of ball bearings are used long enough to experience normal fatigue failure. For example, an ANSI pump is expected to work for 20,000 hours; but the bearings may not. Pump bearings can fail due to overload, excessive wear, weather or substance related corrosion, failure of the lubricant, overheating, or contamination.
Pump bearing issues can also be the result of poor bearing selection for the pump application. If the bearing manufacturer and model number are known, then the fault frequencies for the outer race, inner race, rolling elements, and cage can be determined.
This issue can be prevented by regularly lubricating the bearings with oil mist, specialty oils, or grease.
#6: Misalignment of the Shaft
Because some vibration is normal in pumps, it is best to have a professional repair technician determine if excessive vibration in a pump is due to shaft misalignment. They can also tell you if it is severe enough to affect the pump’s performance and reliability.
Shaft misalignment is not easy to detect and difficult to measure externally. There are no sensors that can be placed on a pump to measure how much force is being used. Pumps with a misaligned shaft can show any of the following:
- Excessive axial or radial vibration
- High temperatures in the casing or near the bearings
- High temperatures of the discharge oil
- Excessive oil leaks at the bearing seals
- Loose coupling or foundation bolts
- Excessive coupling failures
- Breaking or cracking shafts near the coupling hubs or inboard bearings
Conclusion
Spotting a vibration problem early can help avoid unplanned downtimes and allow for a planned pump repair. If you are experiencing one of these vibration problems or another issue with your pump, rotating equipment, or system, contact us. Our modern repair service center is strategically located in southeast Houston and we are capable of handling all of your rotating equipment repair needs.
Share this post: