The Real Cost of Maintenance: Why Proactive Beats Reactive
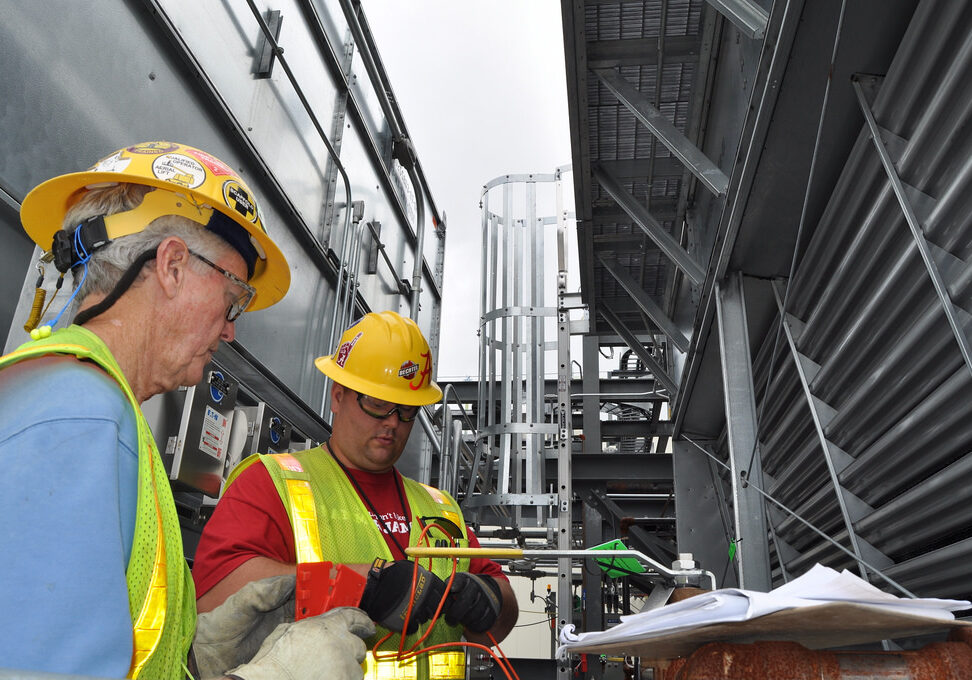
When it comes to asset reliability and operational efficiency, maintenance strategy matters. While some organizations still default to a reactive approach—addressing equipment issues only when failure occurs—industry leaders are shifting toward a more proactive philosophy. Proactive maintenance prioritizes prevention, early detection, and strategic intervention, ultimately extending equipment life, improving safety, and reducing long-term costs.
At Houston Dynamic Services (HDS), we’ve seen firsthand how companies that adopt a forward-thinking maintenance plan gain better control over their operations, reduce emergency repair frequency, and improve asset performance across the board.
Understanding the Difference: Reactive vs. Proactive Maintenance
Reactive maintenance (also known as “run-to-failure” or breakdown maintenance) involves performing repairs only after equipment malfunctions. While it may appear cost-effective in the short term due to minimal upfront investment, this approach often leads to unplanned downtime, costly repairs, safety incidents, and production losses.
Proactive maintenance, on the other hand, includes a combination of preventive, predictive, and condition-based strategies. This involves regularly scheduled inspections, real-time monitoring, and data-driven analysis to detect early signs of wear or inefficiency—allowing interventions before breakdowns occur.
The Financial Impact: Short-Term Savings vs. Long-Term Cost Control
Reactive maintenance may seem economical at first, but over time, the costs quickly escalate. The Marshall Institute reports that maintenance operations relying primarily on reactive methods can end up spending 2 to 5 times more than those with a proactive strategy. Emergency repairs often require premium parts, expedited shipping, and after-hours labor rates—not to mention the cost of halted production.
In contrast, proactive maintenance allows organizations to:
– Schedule downtime strategically
– Extend asset life cycles
– Plan labor and parts in advance
– Avoid costly secondary damage caused by cascading failures
By the Numbers: Industry-Wide Maintenance Trends
A study by Plant Engineering reveals the current state of industrial maintenance strategies in the U.S. While proactive methods are gaining traction, many facilities still lean too heavily on reactive practices:
- 57% of respondents reported that reactive maintenance remains their default approach.
- Less than 50% had implemented any form of proactive or predictive maintenance.
- Only 31% reported using proactive maintenance to reduce unplanned downtime.
The data clearly shows the advantages of moving toward a predictive or condition-based model:
Metric – Predictive Maintenance Users – Reactive Maintenance Users
- Reported energy savings – 45% – 5%
- Reported decreased downtime – 75% – 25%
- Found strategy cost-effective – 55% – 25%
- Reported improved safety – 55% – 5%
These numbers confirm what many maintenance engineers already know: proactive programs deliver measurable benefits in nearly every performance category.
Strategic Benefits of Proactive Maintenance
A proactive maintenance plan doesn’t just reduce costs; it also builds resilience and control into your operations. Key benefits include:
- Increased Equipment Longevity: Routine service prevents accelerated wear, fatigue, and component failure.
- Optimized Equipment Performance: Tuning systems for peak efficiency reduces energy usage and improves throughput.
- Predictable Maintenance Costs: Budgeting for routine service eliminates surprise expenses.
- Improved Scheduling and Planning: Maintenance activities can be coordinated with production schedules to minimize disruption.
- Better Spare Parts Management: Inventory can be stocked based on predictive data, avoiding both overstocking and shortages.
- Compliance and Safety: Regular inspections ensure adherence to industry safety standards and regulations.
- Reduced Downtime: Early identification of wear or imbalance prevents catastrophic failures and associated production loss.
- Operational Transparency: Maintenance KPIs and documentation improve accountability and audit readiness.
How HDS Can Help
At Houston Dynamic Services, we specialize in the support of rotating equipment through precision maintenance, repair, and overhaul services. Our fully staffed service center is equipped with state-of-the-art tools and diagnostics, and our technicians are trained in the latest condition monitoring, vibration analysis, alignment, and thermographic inspection techniques.
Whether you’re looking to transition away from reactive maintenance or enhance an existing preventive program, HDS can help you build a strategy tailored to your plant’s specific assets, demands, and budget. Contact us today to explore how HDS can help you take a more proactive stance and achieve greater performance and reliability from your critical equipment.
Share this post: