Pump Cavitation – What Causes it and How to Prevent it
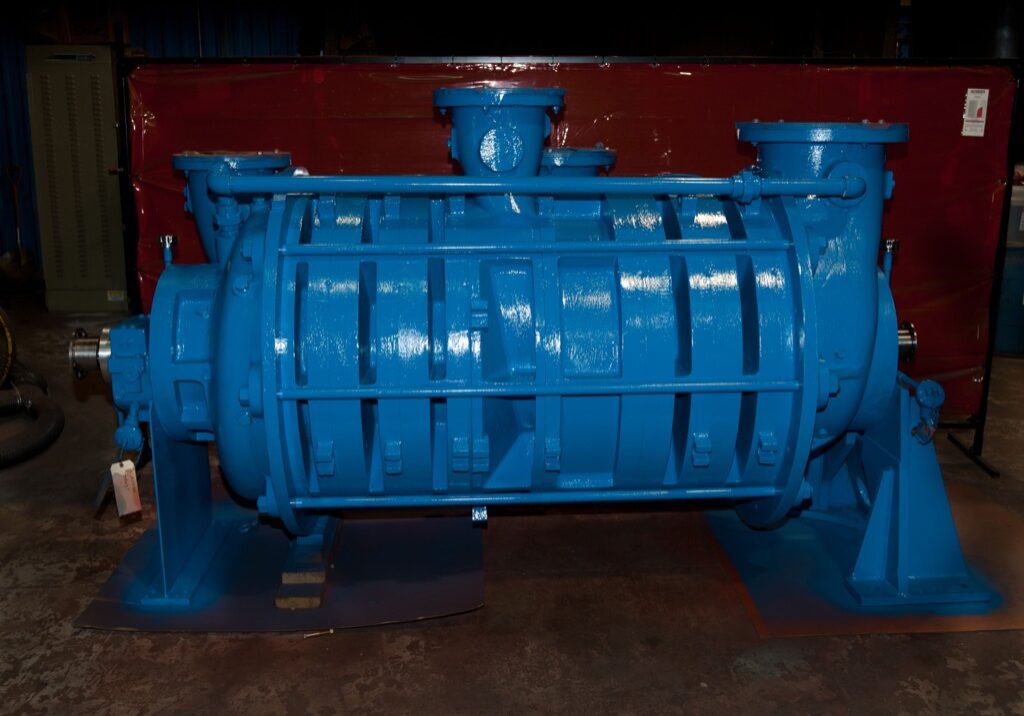
Cavitation can occur in rotating equipment, especially centrifugal pumps. This cavitation can go unnoticed or diagnosed incorrectly. This can lead to issues with production, energy usage, output, lifespan of equipment, and even catastrophic breakdowns. To help with this, we will tell you all about pump cavitation – what causes it and how to prevent it.
What Causes Pump Cavitation?
Cavitation can occur for any number of reasons. One of the most common causes is when the inlet pressure to your pumps is low. Low inlet pressure if often caused by a reduced level of liquid in the tank supplying liquid to the pumping system. Additionally, it can be caused by a leak in the pipes that causes a drop in the inlet pressure.
Pump cavitation can also be caused by vapor bubbles that form and eventually collapse inside the pumped liquid. These vapor bubbles are formed in various scenarios. They can be caused by recirculating currents with high velocity from the impeller, heated liquid, and other areas. A low net positive suction head margin can also cause vapor bubbles. Basically, any operation that causes a pressure drop on the pumped liquid that is below the vapor pressure of the liquid can result in cavitation.
Symptoms of Pump Cavitation
Look for one or more of these symptoms when diagnosing pump cavitation:
- Reduction in pressure or flow – When your pump does not produce the amount of flow as stated by your manufacturer.
- Excessive vibrations: Pump cavitation often comes with strange vibrations in the pump not accounted for by traditional operating parameters.
- Noisy pump: As in the above, noise is often a sign of pump cavitation and is often caused by the pop of the vapor bubbles.
- Impeller corrosion: Cavitation can also damage a pump’s impeller causing pieces to come loose or a noticeable degradation of the impeller itself.
- Failure in the seals or bearings: Premature failures can be caused by pump cavitation.
- Increased power usage: Vapor bubbles can cause your pump to use more power than initially intended. There may also be fluctuations in the power of the pump.
How Can I Prevent Pump Cavitation?
A good and thorough pump and adjoining system’s design is the best step to preventing cavitation. It involves:
- Choosing pumps that are a good fit for your specific needs.
- A pump design with minimal dynamic loss.
- Proper development and implementation of maintenance schedules.
It is also essential to ensure Net Positive Suction Head margins are correct for the specific application. The NPSH value is dependent on the flow of the liquid under your specific conditions. Pumping at high volumes leads to high pressure at the inlet of the pump. Pumping at low volumes increases the risk of cavitation, such as when a tank is being emptied and the pressure to the pump decreases. Each pump has its own NPSH that should be adhered to.
Pump Cavitation – What Causes it and How to Prevent it Using HDS
The Houston Dynamic Supply team can perform diagnostic testing on your pumps to seek out any pump cavitation. We can also diagnose the cause, as well as perform repairs and rebuilds for your replacement parts in our local facility. Contact us speak with our experts about how we can help you address pump cavitation.
Share this post: