Maximize Equipment Reliability with Condition Monitoring
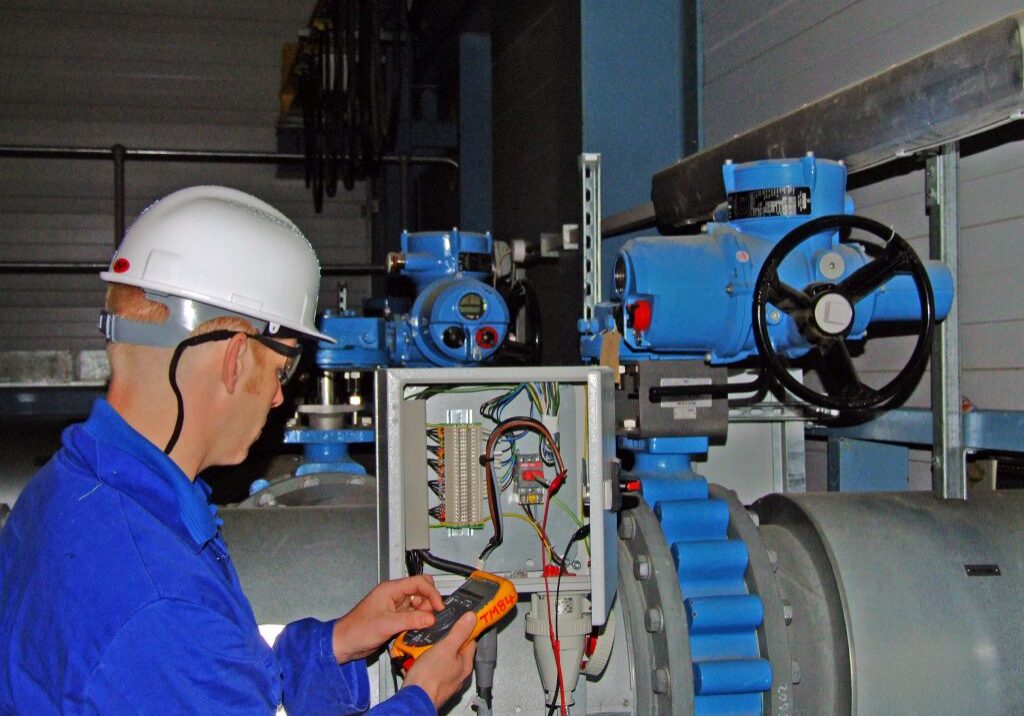
Your equipment was expensive to design, purchase, and install. This does not include the costs to operate, maintain, diagnose, repair, and ultimately replace. But did you know you can maximize equipment reliability with condition monitoring? We will show you how below.
Do I Need Condition Monitoring?
Depending on your operation, your rotating equipment could be some of the more maintenance-intensive equipment. It is often the most likely to experience a failure or some level of decreased operation, on average once a year. We have also found that centrifugal pumps and other rotating equipment in crucial roles can have double or triple setups to function as backups and are programmed to be ready to switch when needed. Condition monitoring is designed to ease all of this.
What is Condition Monitoring?
It is the process of observing equipment to detect signs of potential failures or slowdowns before they happen. Condition monitoring collects performance data and analyzes trends to detect abnormalities in operations. It was a crude practice in the past. However, today’s advanced operations often use smart sensors and other tools to do tasks such as measure vibrations, analyze oil, and monitor operating temperature.
How Does Condition Monitoring Work?
Imagine you have sensors to detect the above. You program your system to monitor the oil. An anomaly is first detected via excessive noise. Then you detect elevated operating temperatures. Your operator notices smoke coming from the system. The system fails. Condition monitoring could instantly tell you when there was excessive noise and in which component to avoid the failure.
What are the Benefits of Condition Monitoring?
Many owners and operators choose condition monitoring for its ability to detect potential failures, avoid unnecessary downtime, and decrease overall operating costs. It does so by:
- Advanced insights – As opposed to older data collection done via periodic inspections that can overlook critical issues, condition monitoring give you up to the minute insights via an advanced platform.
- Predictive maintenance – This data allows you to anticipate equipment failures before they happen and can even extend the life of your critical assets.
- Better decision making – All this data allows you to make better decisions on items such as maintenance, repair, and even replacement. You can even identify and eliminate any bottlenecks in your system.
- Increased safety – Finally, condition monitoring can improve safety by detecting and addressing hazardous issues early. Data on items such as temperature, vibration, output, and others allow you to correct faulty equipment or even program it to shut down under certain conditions. In addition, workers do not have to approach equipment that may be malfunctioning to get readings, or conduct tests.
HDS Helps Maximize Equipment Reliability
The Houston Dynamic team has years of experience in working with all sorts of rotating equipment and is knowledgeable of all sorts of condition monitoring. Bring us your data so we can diagnose, repair, or rebuild your equipment as needed. Contact us and speak with our experts.
Share this post: