How Vibration Analysis Optimizes Predictive Maintenance
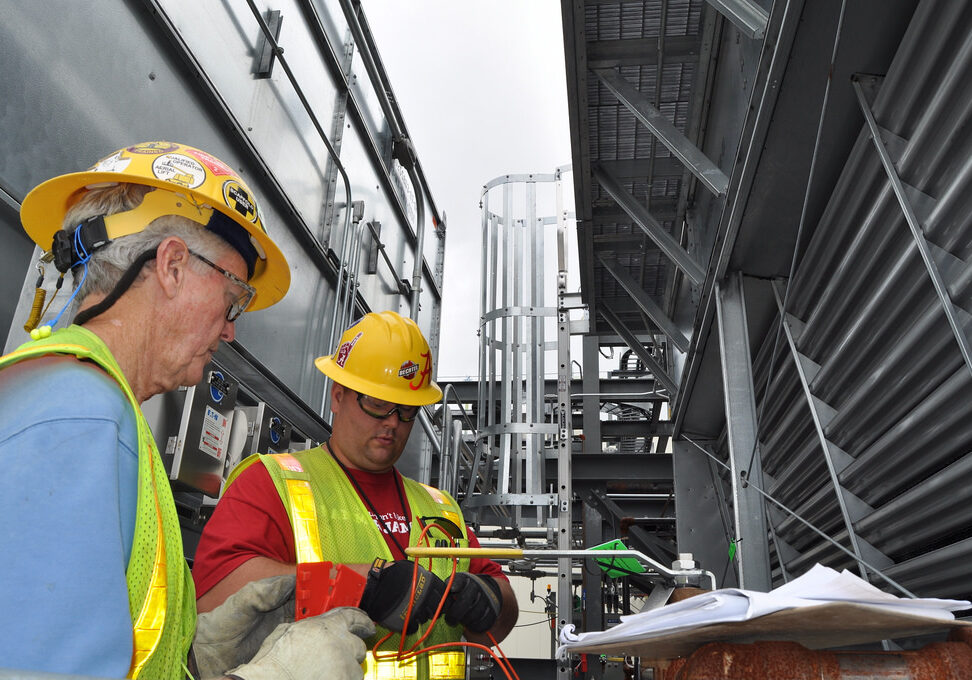
Vibration analysis is one of the most powerful diagnostic tools to help you monitor, identify, and prevent a mechanical failure in your rotating equipment. It is also an essential component of any predictive maintenance because it can detect upcoming issues in machinery before they lead to catastrophic failures and expensive down time.
How Does Vibration Analysis Work?
Vibration analysis involves several steps and begins with using specialized instruments to measure vibrations. This equipment has sensors that measure the vibrational characteristics of your machinery, such as amplitude, frequency, and phase – like how the Richter scale measures the intensity of earthquakes. The data is then analyzed with various tools and techniques such as software that identifies abnormal vibrations and can match them to potential issues, as well as even determine a course of action.
Types of Vibration Analysis
Your machinery can have different types of vibrations including radial, axial, and torsional. Radial vibrations take place perpendicular to the axis. Likewise, axial vibrations occur on the rotating shaft’s axis. Torsional vibrations give off a rotating or twisting motion on the equipment.
Vibrations are also categorized as external or forced. This happens when something outside the system is causing the vibration, such as vibrations in a neighboring pump or motor. Natural vibrations, or resonance, are caused when the natural frequency matches the operating frequency and leads to excessive vibrations.
Causes of Minimal or Excessive Vibrations
Any number of issues can cause vibrations, such as:
- Unbalance identified by deviations in baseline rotation frequency.
- Misalignment, often identified by deviations in baseline rotation frequency.
- Looseness, often identified by deviations in baseline rotation frequency.
- Gear meshing and other cyclical issues identified by harmonics.
- Off balance rotating parts.
- Worn or corroded bearings.
- Worn or corroded seals.
- Too much or too little power to the unit.
- Wrong operating temperature.
- Other structural issues.
The Benefits of Vibration Analysis
There are five reasons vibration analysis optimizes predictive maintenance:
- Early detection of issues to prevent failure.
- Better scheduling of maintenance tasks allows you to prioritize resources.
- Lower costs for maintenance by optimizing the tasks and their frequency.
- Better energy consumption through more efficient performance in your machinery.
- Improved safety outcomes to reduce the instance of breakdowns, leaks, and other hazards.
In addition to the above, vibration analysis can tell you more on the overall health of your machinery, as well as its performance over time.
Assistance with Vibration Analysis
Vibration analysis is not an easy task to perform. Your specialist should have the knowledge and experience for your equipment and industry. HDS has 42 years of experience with vibration analysis, rotating equipment, and much more. Our team offers expert diagnostic, repair, and refurbishing services on all sorts of rotating equipment.
Share this post: