How Root Cause Analysis Can Improve Production Reliability
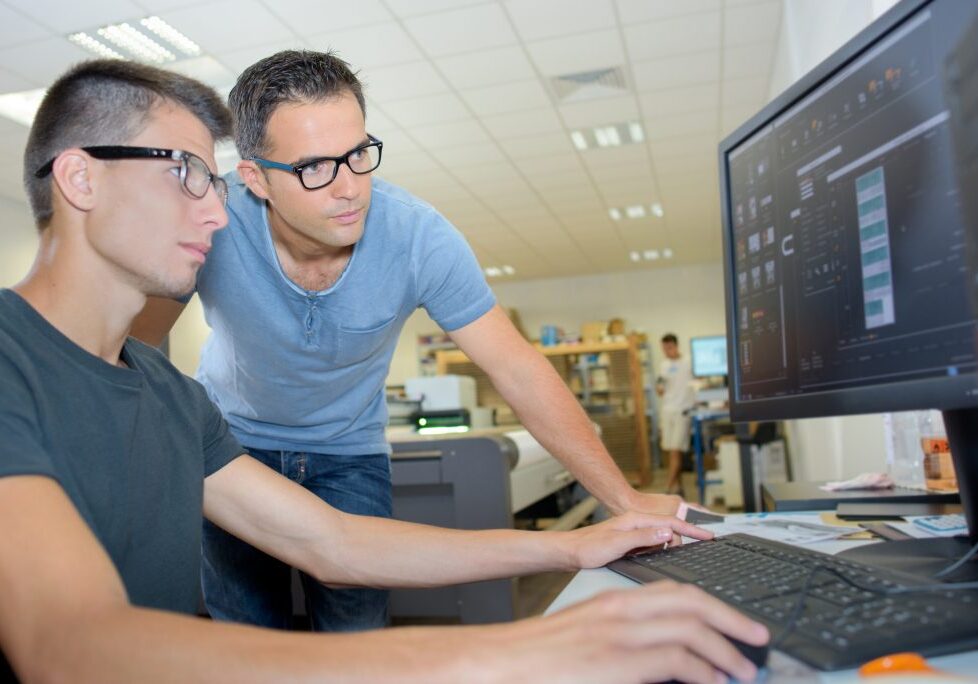
Approximately 20 to 30 % of all industrial maintenance hours are used for Root Cause Analysis, at times called RCA. Time was calculated by counting time used to find cause of problems, elimination, and any reports done at that time. It can also include anything from the time it takes to train operators in new procedures to having engineers design new processes. Below, we will show you how root cause analysis can improve production reliability and be well worth the time you put into it.
What is RCA?
In short, RCA focuses on analyzing the failure in order to eliminate the problem. In too many cases, owners and managers just “go with the usual” when dealing with a common issue without confirming the cause. They may perform maintenance, repairs, or even replace a piece of equipment without identifying the core cause for the breakdown, slow down, or other abnormal operation. Your plant could spend millions in associated costs and increased down time by taking these outdated courses of action – which is why RCA is so important.
Root Cause Analysis Steps
- Critical Thinking – It’s actually acceptable to assume a current failure that presents itself similarly to another in the past may be from the same cause. However, it is essential to confirm the hypothesis. At this stage, you may begin guessing at the potential cause of the failure and create a list of possibilities, but be open to other possible causes.
- Diagnose – Be sure to consult your owner’s manual, as they are full of troubleshooting tips and diagnostic instructions. Pull the data from this machine and others connected in the process – as one of them may affect the machine currently malfunctioning. You should also speak with the operator of the machine to see if they noticed anything off during their work.
- Warranty – Don’t forget that your piece of equipment may be under warranty. Consult the manufacturer ASAP if this is the case and give them all the data collected. This includes warranties from the OEM, manufacturer of any parts you may have had installed, or warranty for any recent work performed.
- Get an Experienced Contractor – If none of the above have identified the root cause and fixed the issue, it’s time to contact an experienced contractor in your area. They have advanced equipment that can detect everything from vibration to operating temperature to electrical issues.Root Cause Analysis Guidelines
RCA can only improve production reliability when an effective solution is developed and implemented. Additionally, this course of action can be logged for future issues in matching equipment. Effective root cause analysis is also complete when the root cause of the issue is understood and proven to all relevant parties. In addition, it is essential to listen to all possible causes.
For example, a power plant in the United States experienced random power outages. All personnel in the plant fervently searched all the equipment for a possible cause – to no avail. Finally, management brought in an operator who determined the cause was the cattle outside the plant. They randomly rubbed against a loose power pole, which caused the cables to come into contact with each other. The loose pole was fixed, and operations returned to normal.
Houston Dynamic Supply Performs Root Cause Analysis to Improve Production Reliability
If your operation needs root cause analysis performed on your rotating equipment, contact our team to help. HDS serves the Gulf Coast and can perform a range of expert diagnostic tasks. Additionally, we repair and rebuild all sorts of rotating equipment, as well as craft custom parts.
Share this post: