3 Top Strategies to Reduce Maintenance Costs
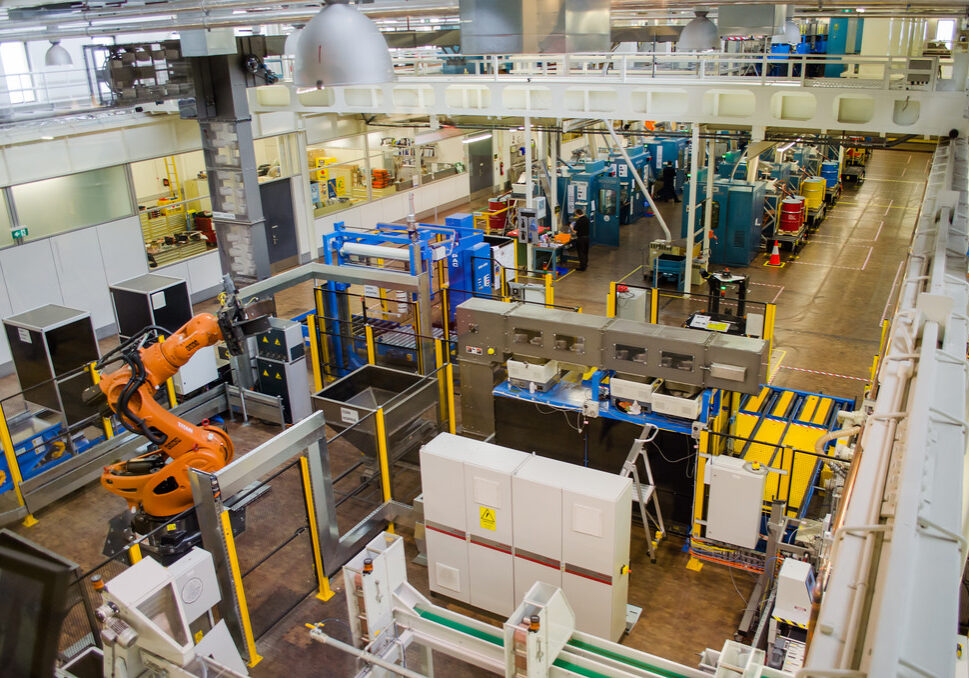
Below, we will show you how to leverage maintenance strategies to minimize the cost of running your facility.
The Japanese Way
The Japanese invented the concept of lean production that reexamines the way maintenance is done in a variety of operations. These practices include but are not limited to:
- Justify the Maintenance – Maintenance should be scheduled by need or perceived risk rather than aesthetics or because a fancy salesman said it should be done. You should perform a detailed analysis on the assets’ critically to validate the cost of maintenance.
- Build Long-Term Working Relationships – No one can run a plant with just their workforce. You will need outside help such as maintenance specialists, turnaround experts, and other third-party contractors. Do your research and get someone who has extensive experience in the field you need, along with engineers. They can help develop a strategy to monitor production, justify the purchase of new technology, design-out problems, and much more.
- Utilize Skills in the Workforce – Choose to use tradesman that are trained in the best-practices in the use of your equipment. They may cost more but will reduce maintenance costs in the long run. You may train operators to perform basic procedures and in-process condition inspections.
- Keep and Constantly Update Data on the Plant – Many new technologies allow owners to view plant data at a glance. Whether you use them or not, it is important to monitor on-condition maintenance including interior inspections and charting process parameters. You should also conduct controlled experiments to determine stable process operation, as well as investigate all root causes to full details with an engineering analysis.
- Continually Improve the Operation – Resting on your laurels is not an option. Your goal should be to use asset history to plan for and justify the expenses associated with improvements. The general practice is to develop a two-year plan using the last eight years of the plant’s history. You should also have mechanisms in place to give feedback on operating experience to projects, an office seating location, and formal meeting agenda items including the above.
Decrease the Request Response Time for Maintenance
It is essential to promptly respond to maintenance requests and prioritize asset service. You may use a coded system that classifies maintenance task by priority. It is best not to use paper-based systems because it may take a supervisor a while to get to them. An electronic request is best so the maintenance task may be instantly read, assigned a priority, and resolved as soon as possible. Your plant should also have floor plans that are up to date on each facility so maintenance personnel know exactly where to go and which piece of equipment to service.
Be Precise
Accuracy is critical in determining when and how to assign maintenance. This includes having data ready such as:
- Machine vibration confirmed as below standard including balance and transfer isolation.
- All shaft alignments to under a hair’s width.
- The assembly should be free of distortion, pinched parts, and soft feet.
- Know when the manufacturer of your asset recommends maintenance should be performed.
You should have accurate data on the condition of the asset at all times including oil, vibration, wear, fatigue/stresses, temperature, as well as the permissible parameters for all of this. If performing a maintenance task to address an issue with one of these, be sure it addresses the root cause of the issue.
Houston Dynamic Repairs and Maintenance
We are experienced equipment repair and maintenance experts located in Houston who can test and perform advanced maintenance tasks on the components of your machines, as well as build replacement parts. Contact us today with your equipment maintenance needs.
Share this post: