3 Tips for Implementing a Predictive Maintenance Program
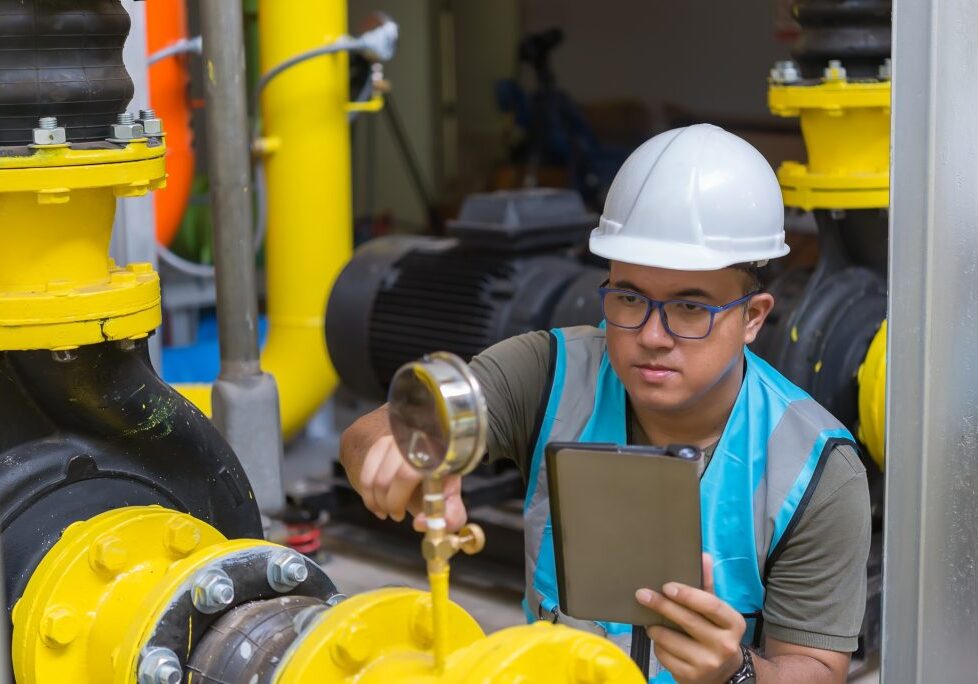
HDS is a huge fan of proper maintenance, with a focus on predictive rather than reactive maintenance. This approach comes with many benefits in both reduced down time and more efficient uses of maintenance resources. Below we will share 3 expert tips for implementing a predictive maintenance program.
- Prioritize Your Assets
The first part to a successful predictive maintenance program begins with identifying and prioritizing all your critical assets. We recommend you gather all maintenance costs and breakdown records to conclude which equipment fails will cost the most. In our experience, we have seen that data analysis of past events can reveal future patterns, which inform your predictive maintenance. Focus on high value assets and their data to create failure modules, their effects, and a plan for improved inspection, testing, and maintenance.
- Identify Key Performance Indicators
The data collected above will reveal key performance indicators (KPIs), such as excessive vibration in a piece of rotating equipment that is about to fail. KPIs are specific to equipment, application, and industry. However, many standard KPIs include vibration, pressure, temperature, power usage, and RPMs for rotating equipment. These indicators are used to detect deviations from ideal operating conditions, which can be signs of upcoming failures.
For example, we have clients who maintain data on vibration levels in rotating equipment. Any deviation is often the sign of an imbalance or misalignment that can lead to damage in the internal components, the piece of equipment itself, and possibly the entire system. We recommend you constantly evaluate and update your key performance indicators as new technology emerges to keep your program ahead of your demand.
- Utilize the Latest Technology
One of the best developments in industry is the availability of smart devices designed to monitor conditions in all sorts of facilities. This includes the continuing development of condition-monitoring sensors that can keep track of all your KPIs in one place. In fact, some are designed with recommended key performance indicators for certain equipment and applications. Additionally, you may also utilize Internet of Things (IoT) devices, that work in conjunction with your system and provide additional security measures.
One of the best benefits of utilizing the latest technology for predictive maintenance is that you get real-time data in addition to creating invaluable historical data each and every day the tech is in use. We have seen that clients who properly use the latest tech see a significant reduction in both minor and major breakdowns and are able to develop a comprehensive predictive maintenance program.
How HDS Can Help
The Houston Dynamic Supply team can help any predictive maintenance program by performing advanced inspections and diagnostic testing on your rotating equipment to identify any hazards. We can also take data on your KPIs to help develop a maintenance plan, as well as perform repairs and rebuilds in our local facility. Contact us to speak with our experts about how we can help your predictive maintenance.
Share this post: