Equipment Series: Compressors
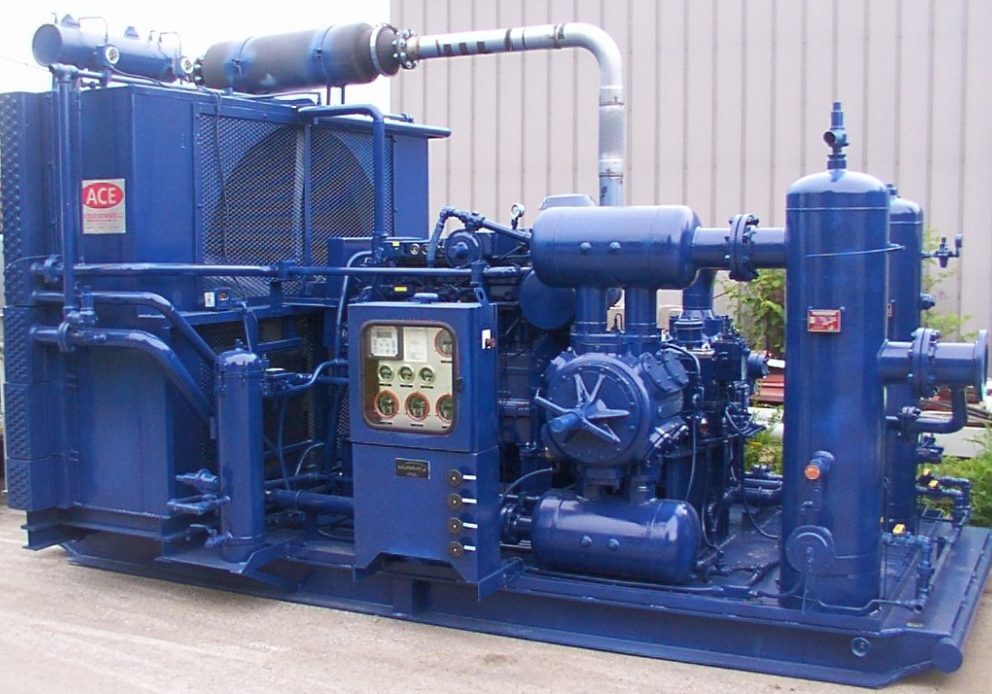
In the second installment of our Equipment Series, we will be focusing on compressors. In a nut shell, compressors are devices that increase gas pressure by reducing its volume. They are similar to pumps because they are designed to use increased pressure to move media. However, compressors are generally associated with moving gaseous media, while pumps usually move liquids.
Types of Compressors
Compressors come in both positive displacement and dynamic models. They are used in many industries and in many applications. There are four major types of compressors used in the refining, power generation, petrochemical, and offshore drilling industries.
Positive displacement compressors
Reciprocating compressors – These compressors use a piston inside a cylinder to compress air. Various automatic spring-loaded valves open when the desired differential pressure is achieved across the valve. Inlet valves open when the cylinder’s pressure goes below the intake pressure and discharge when the cylinder’s pressure goes above the discharge.
Screw compressors – These compressors use two or more counter-rotating screws which take in gas from the inlet valve. The turning of the screws moves the gas to the other end of the compression chamber. It grows smaller as the air travels through it to increase its pressure. The process is one continuous motion that produces less pulsing or surging than reciprocating compressors.
Dynamic compressors
Centrifugal compressors – These compressors generally use an inlet, impeller, diffuser, and collector. At times called radial compressors, they work by adding kinetic energy with an impeller or rotor to achieve a continuous flow of media. The kinetic energy is converted to an increase in pressure through a diffuser by slowing its flow.
Axial flow compressors – Flow generally enters and exits the compressor parallel to the rotation axis. Rotating airfoils in the rotor accelerate the media to increase its pressure. It is then diffused by stationary blades and at the compressor’s exit to control its exit guide vanes (EGV).
Applications for Compressors
In addition to the aforementioned industries, compressors are commonly known to be used in the HVAC industry to compress and cool or heat air. Compressors are also used in other heavy industries such as:
- Aerospace
- Chemical
- Marine
- Medical
- Plastic
- Research
- Transportation
- Refrigeration
- Welding
Problems With Compressors
Compressors need to be inspected and maintained on a regular basis. It is essential for a compressor to produce enough cubic feet per minute (CFM) in compressed air to operate per the manufacturer’s specifications. CFM is one of the most important factors when choosing and maintaining a compressor. Many systems can fail due to incorrect CFM.
Because they are sensitive pieces of equipment, they can fail due to any number of factors. These include but are not limited to:
- Insufficient power
- Surges in power
- Dirty coils
- Obstructed suction and/or lines
- Incorrect suction pressure
- Contaminants in system
- Low coolant levels
- Low oil levels
- Improper operating temperature
- Not having a proper compressor overload
Conclusion on Compressors
At Houston Dynamic Service, we have extensive knowledge on how to repair and rebuild all types of compressors from all OEMs. To learn more, contact us to discuss how we can keep your Compressors running at their best.
Share this post: