The Role of Proper Lubrication in Rotating Equipment Performance
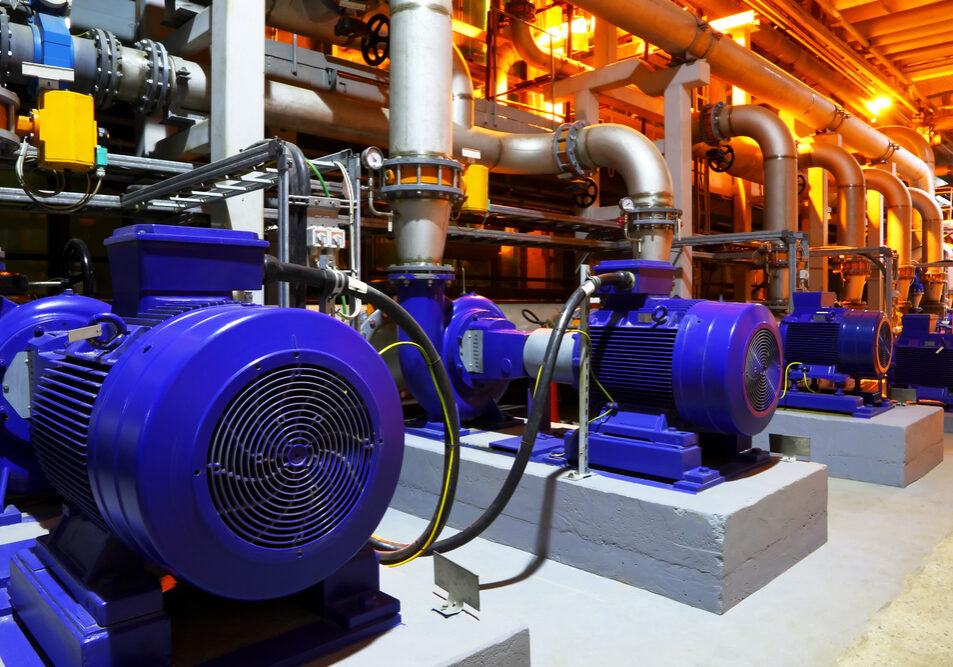
Is your rotating equipment experiencing frequent overheating, unusual noises, or unexpected shutdowns? Perhaps you’ve noticed smearing, discoloration, or other warning signs of mechanical distress. These symptoms often point to inadequate lubrication—a common but preventable issue in the maintenance of rotating machinery. Ensuring proper lubrication is critical for maximizing equipment reliability and minimizing downtime.
Why Lubrication Matters
Lubrication is the lifeblood of rotating equipment, influencing its efficiency, longevity, and reliability. Studies reveal that two primary causes of equipment failure are insufficient lubrication and contaminated lubricants. These issues can lead to unnecessary wear, higher operating temperatures, and shorter intervals between repairs.
In environments like refineries, where equipment operates under demanding conditions, the consequences of poor lubrication can be costly—not just in terms of repairs but also production delays. A robust lubrication strategy allows equipment to run cooler, last longer, and achieve higher mean times between failures (MTBF), making it an essential focus for any reliability program.
What Proper Lubrication Achieves
The benefits of effective lubrication extend beyond just keeping machinery running. It ensures:
- Friction reduction, which allows parts to move smoothly and efficiently.
- Minimized wear on components, reducing the risk of premature failure.
- Corrosion protection, safeguarding equipment from chemical and environmental damage.
- Heat dissipation, preventing overheating and maintaining optimal operating conditions.
- Debris control, keeping contaminants from interfering with performance.
These outcomes are crucial for maintaining uninterrupted operations and extending the service life of critical equipment.
Critical Considerations for Lubrication Management
To optimize lubrication in rotating equipment, engineers must carefully consider several factors, including viscosity, lubricant type, application methods, and the amount used.
1. Viscosity
Viscosity is one of the most important properties of a lubricant. It determines the lubricant’s ability to form a protective film between moving parts and carry loads effectively.
- Low Viscosity: Suitable for fast-moving components, but it may fail under high temperatures, leading to wear and metal contact.
- High Viscosity: Ideal for slow-moving, heavy-load applications but can cause resistance in low-temperature conditions, increasing energy consumption and oxidation risks.
Key Insight: Always consult the equipment’s OEM manual to identify the recommended viscosity for your operating conditions. In refinery operations, where extreme temperatures are common, selecting the right viscosity is especially critical.
2. Lubricant Types
The choice of lubricant—whether oil or grease—depends on operating speed, temperature, and equipment requirements:
- Grease: Effective for sealing and protecting components, but it may not dissipate heat as well as oil.
- Oil: Offers better heat dissipation and flow characteristics, particularly in high-speed applications. Synthetic oils, in particular, excel in extreme environments due to their stability and resistance to oxidation.
Best Practice: Synthetic lubricants are increasingly preferred in refinery applications for their durability and ability to handle harsh conditions. However, the cost-benefit ratio should always be evaluated.
3. Lubrication Methods
The method of applying lubrication varies based on the equipment and its operational demands. Common approaches include:
- Oil Mist Systems: These centralized systems atomize oil and distribute it as a mist, ensuring consistent lubrication across multiple components. Ideal for high-temperature and high-speed equipment, oil mist systems also help reduce contamination risks.
- Splash Lubrication: Involves submerging parts in oil or using oil rings to distribute lubricant. It’s effective but requires regular monitoring to maintain the correct oil levels.
- Grease Lubrication: Often used for bearings, grease is easy to apply but less effective at dissipating heat, making it better suited for moderate-speed or intermittent operations.
Tip for Engineers: Consider automating lubrication methods in high-demand environments to improve precision and reduce human error.
4. Quantity of Lubricant
Applying the correct amount of lubricant is just as important as choosing the right type. Over-lubrication can increase resistance and generate excess heat, while under-lubrication can lead to metal-to-metal contact and equipment seizure.
Guideline: Use automated systems or regular inspections to ensure lubrication levels remain optimal. Refinery engineers should prioritize consistency to avoid costly equipment failures.
Proper lubrication is foundational to rotating equipment reliability. By prioritizing correct viscosity, selecting the appropriate lubricant type, and using effective application methods, engineers can significantly reduce downtime, extend equipment life, and maintain operational efficiency.
At Houston Dynamic Service, we specialize in servicing and optimizing rotating equipment for refineries, chemical plants, and manufacturing. With over 35 years of expertise, we provide tailored solutions to ensure your equipment operates at peak performance. Contact us today to learn how we can help support your maintenance and reliability goals.
Share this post: