The Critical Role of Alignment in Turbine Preventive Maintenance
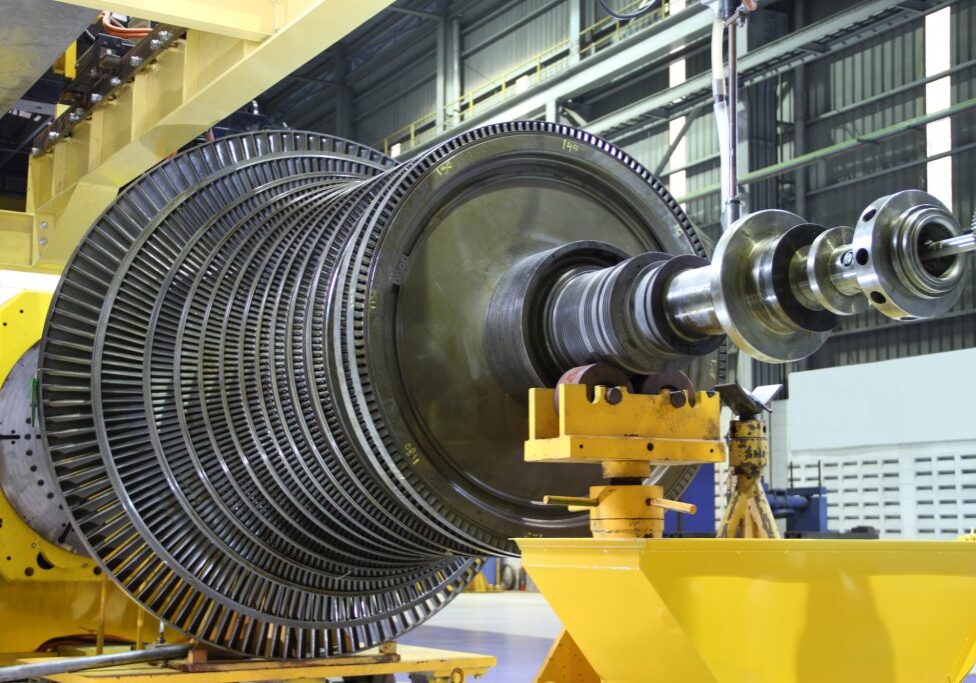
Alignment is one of the most critical, yet often overlooked, aspects of turbine maintenance. For Maintenance Managers, Maintenance Engineers, and Plant Managers, ensuring proper alignment is vital for the longevity, efficiency, and reliability of turbine systems. Misalignment can lead to catastrophic failures, increased downtime, and significantly higher repair costs. In this article, we will explore the technical importance of alignment in turbines, the consequences of poor alignment, and the best practices for maintaining precise alignment during preventive maintenance.
The Importance of Alignment in Turbines
Turbines are complex machines that convert energy from fluids into mechanical energy, often used to generate electricity or drive other critical machinery. The rotating components of a turbine, including the shaft, rotor, and bearings, are subjected to extreme stresses and forces during operation. As a result, precise alignment of these components is crucial to ensure that the turbine operates at optimal efficiency and remains reliable over time.
Alignment refers to the positioning of components to ensure they are properly aligned along the same rotational axis. When components such as the rotor and stator are misaligned, it can lead to several operational issues. The key objectives of alignment are to minimize wear and tear on moving parts, ensure efficient energy conversion, and reduce unnecessary strain on the entire turbine system.
Consequences of Poor Alignment
The implications of poor alignment can be severe, affecting both the performance and the lifespan of the turbine. Misalignment can cause:
- Excessive Wear and Tear on Components
Misalignment results in uneven forces on turbine components, particularly on bearings, shafts, and seals. This leads to accelerated wear on these critical parts, shortening their lifespan and increasing the frequency of repairs or replacements. Misaligned turbines often experience additional vibration, which compounds wear and fatigue, leading to failures in bearings, seals, and other parts that are not designed to handle such forces. - Increased Vibration and Stress
A misaligned turbine experiences higher levels of vibration, which directly impacts the operational efficiency of the system. These vibrations not only reduce the efficiency of the turbine but can also lead to further misalignment, creating a vicious cycle of escalating damage. The increased stress on the components, especially in rotating machinery, can result in cracks or deformations, which can cause severe downtime and costly repairs. - Energy Loss and Reduced Efficiency
Misalignment causes uneven distribution of loads across the turbine components, which reduces the system’s overall efficiency. The misalignment forces the turbine to work harder, leading to increased friction and energy loss. This inefficiency can significantly affect operational costs, especially in large-scale industrial operations where turbines are central to power generation or mechanical work. - Premature Failure of Bearings and Seals
Bearings and seals are particularly vulnerable to misalignment. If the shaft is misaligned, it places additional stress on the bearings, causing them to wear out more quickly. In severe cases, the misalignment can cause the bearings to fail entirely, leading to shutdowns and expensive repairs. Similarly, seals that are not properly aligned may fail to contain fluids or gases effectively, resulting in leaks that could damage other parts of the turbine and surrounding equipment. - Operational Downtime
Poor alignment often leads to unplanned maintenance or unscheduled shutdowns. The increased vibration and wear can cause turbines to fail during operation, leading to downtime. The cost of downtime in industrial environments is significant, affecting productivity, revenue, and overall plant performance.
Best Practices for Turbine Alignment in Preventive Maintenance
To avoid the detrimental effects of misalignment, it’s essential to establish robust procedures for turbine alignment as part of your preventive maintenance program. Proper alignment during installation and regular alignment checks are critical for ensuring the longevity and efficiency of turbines.
- Use Precision Tools for Alignment
Advanced alignment techniques require the use of precision measurement tools such as laser alignment systems, dial indicators, and optical alignment devices. Laser alignment systems are particularly effective because they provide high levels of accuracy, measuring minute deviations in alignment without the need for physical contact. This method ensures that turbines are aligned to within the tolerances specified by manufacturers and operational standards. For high-precision applications, these tools can measure misalignment in both the vertical and horizontal axes.
- Regular Monitoring and Adjustment
Alignment should not be a one-time process; it requires ongoing monitoring and adjustment. Maintenance teams should regularly check alignment at key points in the turbine system. This includes checking the alignment of the turbine shaft, rotor, bearings, and other moving components. During routine inspections, the alignment should be evaluated using laser or dial indicators to detect any deviations. If misalignment is detected, adjustments should be made before it leads to further damage.
- Control External Environmental Factors
Factors such as temperature fluctuations, foundation settlement, and vibrations from nearby equipment can cause misalignment in turbines. It is crucial to control these external environmental influences as part of your alignment strategy. For example, the turbine’s foundation should be inspected periodically to ensure that it remains stable and level. Any settlement of the foundation could lead to misalignment, which should be addressed immediately. Additionally, vibration analysis tools can be used to monitor vibrations from nearby machinery, which may contribute to misalignment.
- Optimize Shaft and Bearing Alignment During Installation
Proper alignment during installation is the first and most crucial step in ensuring long-term turbine reliability. When setting up a new turbine or reinstalling after repairs, the shaft and bearing alignment must be carried out meticulously. During installation, care should be taken to ensure the rotor and stator components are centered and aligned. The shaft should be mounted on well-aligned bearings to ensure smooth rotation and minimal friction during operation.
- Train and Develop Skilled Technicians
The accuracy of turbine alignment is highly dependent on the skill of the technicians performing the work. Maintenance teams must be trained in the use of precision alignment tools and the principles of turbine operation. This ensures that they are capable of identifying potential misalignment issues early and making precise adjustments. Well-trained technicians also know how to interpret vibration data and use it to detect misalignment or imbalance in the system.
- Implement Vibration Analysis
Vibration analysis is an essential diagnostic tool for detecting misalignment in turbines. Routine vibration testing can identify misalignment before it causes severe damage. High levels of vibration are often the first sign of misalignment, and early detection allows for corrective measures to be taken quickly. Vibration sensors installed on key turbine components provide real-time data, which can be analyzed to monitor alignment and overall equipment health.
Proper alignment is not just a maintenance task; it is a critical aspect of ensuring the reliability, efficiency, and longevity of turbine systems. Misalignment, if left unaddressed, can lead to excessive wear, energy loss, and catastrophic failure. By implementing rigorous alignment procedures, including the use of advanced precision tools, regular monitoring, and technician training, plants can significantly improve the performance and lifespan of their turbines.
For Maintenance Managers, Maintenance Engineers, and Plant Managers, making alignment a cornerstone of your turbine preventive maintenance strategy is essential for avoiding costly downtime and ensuring smooth, reliable operation. By taking a proactive approach to turbine alignment, you can optimize the efficiency of your machinery and extend the operational life of critical equipment, ultimately improving the bottom line and ensuring plant safety and productivity.
Share this post: