Pump Impeller Imbalance – One of the Top Six Pump Vibration Problems
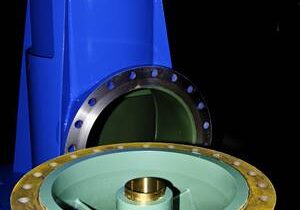
We have previously shared the top 6 vibration problems that lead to inferior pump performance. In this article we’ll discuss one of the more difficult ones: pump impeller imbalance. A number of factors can cause a pump’s impeller or other components to become imbalanced including improper use, collision with other equipment, and even normal wear and tear. This imbalance puts undue pressure on the pump and over time can cause poor performance, inefficient energy usage, and a shortened lifecycle.
What is Pump Impeller Imbalance?
There are two main types of pump impeller imbalance, single and two plane.
Single plane imbalance – Also called force or static imbalance, it is similar to visualizing a disc shaped part with a weight taped to the edge. When the disc is lifted, it will turn and come to rest with the weighted part facing down. When the disk is spun, whatever it is attached to shakew as it attempts to rotate the weight around, causing an imbalance at another point rather than at its intended point. The disc could also wobble as it spun around the shifted center of mass.
Two plane imbalance – This is also referred to as couple imbalance. Visualize the entirety of an automobile wheel’s rim both visible and invisible. If you were to attach a weight to one end of the cylinder and the other but offset them 180 degrees from each other, this would resemble a two plane imbalance. If the rim were lifted off the ground, it would not rotate in the same fashion as the single plane disc. This rim would wobble as it rotated even though it is no longer parallel to the geometric axis.
How is Pump Impeller Balance Performed?
Pump impeller balance is the procedure in which the rotor’s mass distribution is examined and adjusted to ensure the vibration of the journals and/or forces on the bearings correspond to service speed and are within the specified limits.
The International Standards Organization (ISO) has certain guidelines regarding a number of ways to balance different kinds of devices. For pump impellers, they recommend a balance grade of G-6.3. This grade is achieved by balancing a rotor that runs at 3600 rpm to a value of 0.01 ounce-inches per pound of weight. These ISO standards contain many detailed methods of calculating single plane and two plane imbalance tolerances that are dependent on the part’s ratio of its diameter to its length.
Other Methods to Correct Pump Impeller Imbalance
Pump impellers can also be balanced by removing material, drilling, grinding, or milling. In addition, horizontal overhung balancers can be modified with grinding correction. This method works by spreading the material removal process across a large area with minimal depth. Pumps can also be equipped with correction devices and automatic correction cycles.
Conclusion on Pump Impeller Imbalance
Precision pump impeller balancing coupled with expert assembly of impellers can result in a smooth and quiet piece of equipment. A minimal investment can result in many months, or even years of added service along with improved energy consumption.
Identifying and implementing the optimal solution for a pump’s impeller imbalance requires skill and experience. Early detection prevents prolonged and unplanned downtimes. If you are experiencing a pump imbalance problem, contact us for a quick response and creative solutions. Our modern repair facility is strategically located in southeast Houston and we have the capabilities and expertise to handle all of your rotating equipment repair needs.
Share this post: