Pump Flow Pulsation – One of the Top Six Pump Vibration Problems
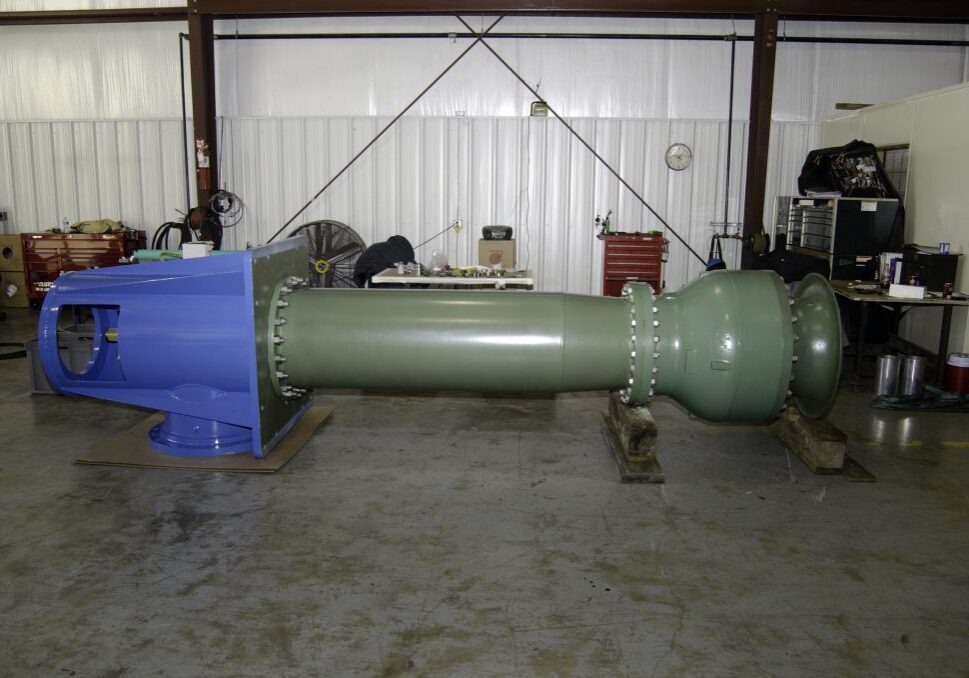
Previously, we discussed the top 6 vibration problems that cause pumps to underperform or fail altogether. In this entry, we will discuss the issue of pump flow pulsation. Pulsation is the result of uncontrolled pressure waves caused by a change in flow. Media in a pump has a mass and there are required acceleration forces needed to move it. Once in motion, media will remain so as the force is sufficient and friction is minimal. This force is not absorbed by the media but rather is transferred through it. Any unbalance in the media’s mass and force can generate destructive forces that may lead to pump flow pulsation, which can cause catastrophic component or entire system failure.
Causes of Pump Flow Pulsation
Pulsation can at times be confused with surge, or a phenomenon where a sonic wave is created in a pump – usually in those that close in less than 1.5 seconds. Pump flow pulsation occurs when there is rapid uncontrolled acceleration and deceleration of energy. This energy is usually slugs of liquid moving and can be designated by frequency and pressure amplitude.
In peristaltic pumps, pulsation is caused as fluid enters the head and becomes trapped between two rollers. It creates a sort of pillow and is followed by a void. When these pillows and voids alternate, it causes fluid flow to cease being smooth and makes it pulsate. Some applications are more susceptible to flow pulsation in peristaltic pumps. These applications can be smoothened by:
- Mounting multiple pump heads at the offset
- Using pump heads with offset occlusion and multiple-roller design
- Changing the configuration of the pump’s discharge tubing
Equipment affected by pump flow pulsation may have any of these signs:
- Gurgling or churning noises
- Metallic sounds
- Thud sounds
- Regularly inconsistent flow
- Pressure waves, especially when the valve is opened
How to Fix Pump Flow Pulsation
One of the most common ways to address pump flow pulsation in most pumps is to install a pulsation dampener. This piece of equipment is geared towards the pump it goes with and is often installed into the discharge line. As the pulsating flow enters the dampener, the air pocket trapped above the fluid can absorb up to 90% of pulsation. This results in a smoother flow leaving the pump. A pulse dampener can be made in all tubing sizes using a retaining vessel and appropriately sized fittings. The dampener’s outlet should be at the same or lower height than the inlet to reduce dead volume.
Pump flow pulsation can also be reduced by adjusting the channel’s configuration in which the tubing flows. Extending the discharge tubing’s length several times and choosing a softer tubing material can reduce pulsation by up to 60%. The softer tubing assists in absorbing pulsation, with the longer discharge line increasing friction. This increases back pressure, compresses the pulses together, and reduces overall pulsation.
If you have a piece of equipment that is showing signs of pump flow pulsation, contact us. Our modern repair facility is strategically located in southeast Houston and we are capable of handling all your rotating equipment repair and maintenance needs.
Share this post: