Maximizing Operational Efficiency: The Case for Energy-Efficient Capital Equipment
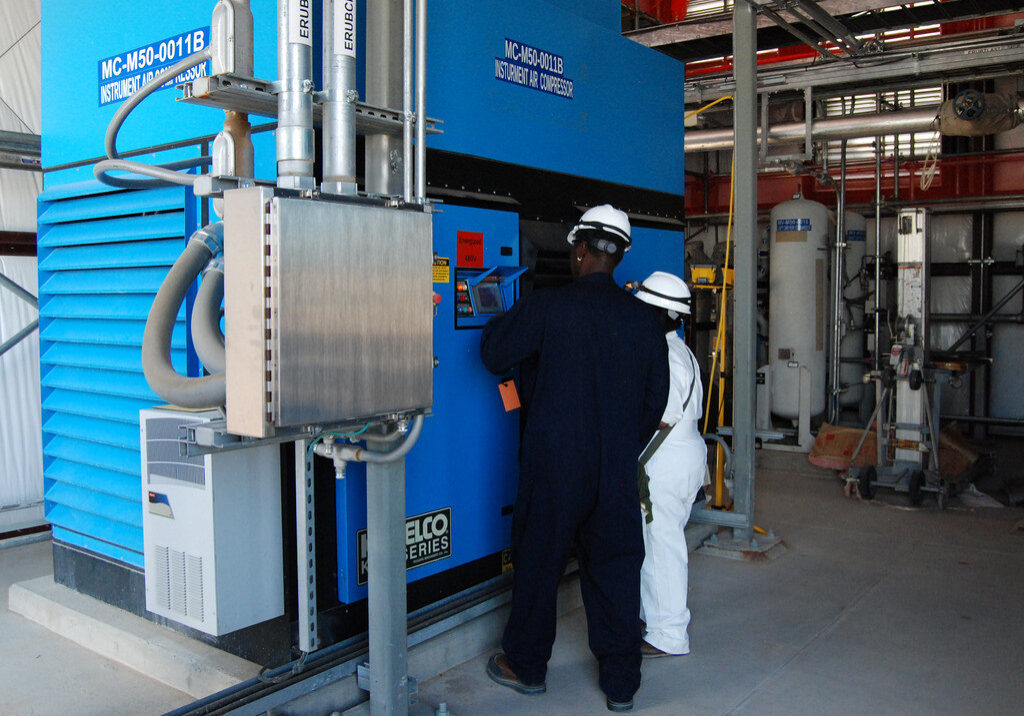
As energy costs continue to rise, industrial companies are under increasing pressure to reduce their consumption and lower operational costs. Energy efficiency isn’t just a buzzword—it’s a critical factor in achieving sustainable operations, enhancing profitability, and complying with evolving regulations. For maintenance managers, engineers, plant managers, and other personnel overseeing capital equipment like industrial pumps, compressors, and turbines, upgrading to energy-efficient systems offers substantial long-term benefits, including reduced energy costs, lower maintenance expenditures, and improved equipment lifespan. In this article, we’ll explore how energy-efficient equipment can directly impact your bottom line and help you navigate the rapidly changing landscape of industrial energy use.
Energy Efficiency: A Game Changer for Industrial Operations
Industrial facilities, especially those in manufacturing, account for a significant portion of energy consumption in the U.S.—nearly one-third. Electrical costs alone can comprise over 25% of a facility’s total energy expenditure, with pumps, compressors, and motors being some of the biggest culprits. While energy efficiency may once have been considered an issue for consumer electronics and household appliances, the shift toward efficient industrial equipment is now an essential strategic consideration. Upgrading older systems to more energy-efficient models can lead to energy cost reductions of up to 50%, while also offering a range of state and federal tax incentives aimed at encouraging these investments.
Reducing Energy Consumption: Direct Impact on Operational Costs
The cost-saving potential of energy-efficient systems cannot be overstated. Consider the energy consumption of inefficient pumping systems, which can waste a significant amount of electricity. A 1996 study examining 1,690 industrial pumps revealed that most of them were operating at a dismal 40% efficiency, with some performing at less than 10%. This level of inefficiency not only impacts energy bills but also limits operational reliability, increases wear and tear on equipment, and shortens the lifespan of critical machinery.
Historically, the focus of pump design was primarily on mechanical performance, but recent federal regulations have shifted the industry’s focus toward overall system efficiency. This regulatory shift has resulted in major improvements in pump designs and has highlighted the need for systems that operate closer to their Best Efficiency Point (BEP), ensuring pumps operate at optimal capacity with minimal energy waste.
Key Areas of Improvement for Energy-Efficient Pumps:
Variable Speed Drives (VSDs): Eliminating bypass mechanisms and throttling valves by implementing VSDs ensures that pumps operate closer to their BEP, allowing for better flow regulation and energy savings.
- Optimized Process Design: Reducing the motor load through better process design minimizes unnecessary energy consumption.
- Load and Component Size Matching: Ensuring that pump capacity matches the system’s load requirements helps maintain efficiency and prevents energy loss from oversized or underutilized equipment.
By adopting these design innovations, industrial operations can expect pumps to become more reliable, efficient, and cost-effective. In fact, pumps often account for 5-10% of total ownership costs, and upgrading to more energy-efficient systems can significantly enhance speed regulation, improve flow control, extend equipment lifespan, and reduce long-term maintenance expenses.
Capitalizing on Tax Incentives for Energy-Efficient Equipment
Energy-efficient equipment isn’t just a smart operational investment—it can also yield significant financial benefits through available tax incentives. The industrial sector, as the largest consumer of energy in the U.S., stands to gain the most from federal, state, and local initiatives designed to reduce energy consumption.
Sales Tax Exemption: Many states offer sales tax exemptions for energy-efficient equipment purchases. For example, purchasing energy-efficient pumps, motors, or compressors may qualify your business for an exemption, helping you save on upfront equipment costs.
Additional Tax Incentives: In addition to sales tax exemptions, various other incentives are available at the state and federal levels, including:
- Investment Tax Credits (ITCs): These credits can reduce the amount of federal tax liability for businesses investing in qualifying energy-efficient equipment.
- Accelerated Depreciation: Industrial equipment purchases may be eligible for accelerated depreciation, allowing businesses to write off the equipment’s cost over a shorter period, improving cash flow.
- Production Incentives: Certain energy-efficient upgrades may qualify for production incentives that reward your company for reducing energy consumption or generating renewable energy.
- Property Tax Abatement: Some states offer property tax exemptions for energy-efficient equipment, reducing the long-term cost of maintaining your industrial equipment.
By taking advantage of these incentives, companies can offset the costs of investing in energy-efficient systems, which ultimately contribute to improved profitability.
Looking Ahead: The Future of Energy-Efficient Equipment
The trend toward energy efficiency is not a passing phase—it’s a fundamental shift that is shaping the future of industrial operations. As energy costs continue to climb and environmental regulations tighten, energy-efficient equipment will become even more critical to maintaining competitive advantage and operational sustainability. Incorporating energy-efficient systems into your plant is no longer just an option; it’s a necessity for maintaining profitability while reducing environmental impact.
The benefits of energy-efficient equipment extend beyond just reducing energy costs. They include:
- Reduced Operational Downtime: More efficient equipment requires less maintenance, leading to fewer unscheduled shutdowns and longer operating lifespans.
- Enhanced Compliance: As regulatory pressure increases, adopting energy-efficient practices ensures that your facility remains compliant with industry standards and environmental regulations.
- Environmental Responsibility: By reducing energy consumption, your plant contributes to overall environmental sustainability, helping your company meet corporate social responsibility (CSR) goals.
Incorporating energy-efficient pumps, compressors, turbines, and other capital equipment into your plant’s infrastructure is an investment in both your bottom line and the future of your operations. The savings generated from reduced energy consumption can quickly outweigh the initial investment, providing a solid return on investment (ROI) over time
Start Investing in Energy Efficiency Today
For maintenance managers, engineers, and plant managers tasked with managing capital equipment, the case for energy efficiency is clear. Upgrading to more efficient systems can reduce operational costs, lower energy consumption, extend equipment lifespan, and enhance overall system performance. Additionally, the availability of tax incentives and regulatory pressures make now the ideal time to begin investing in energy-efficient technologies.
At Houston Dynamic Services, we specialize in providing industrial equipment solutions designed to optimize performance and minimize energy use. If you’re ready to take the next step in improving the efficiency of your capital equipment, contact us today to learn more about our energy-efficient products and solutions. Let us help you reduce costs, increase reliability, and build a more sustainable future for your facility.
Share this post: