How Proper Lubrication Can Minimize Rotating Equipment Repair
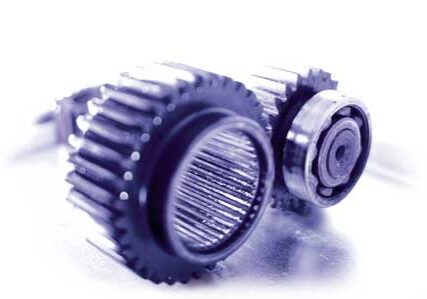
Does your rotating equipment overheat repeatedly or completely seize up? Maybe you have noticed your equipment is making more noise than before. Is your equipment smearing? Is it discolored? Rotating equipment that is not adequately lubricated will not function properly. Adhering to a regular lubricating maintenance schedule is necessary to keep your rotating equipment functioning at its optimum levels. The two largest causes of rotating equipment failure are inadequate lubrication and lubricant contamination. Properly lubricated equipment will operate for longer periods, at lower temperatures, and extending the mean time between repairs (MTBR).
The point of lubricating moving parts is to:
- Decrease or eliminate friction
- Reduce wear
- Protect from corrosion
- Absorb heat
- Reduce noise
- Prevent damage from debris
All of these results of poor lubrication lead to serious downtime and preventable costly repairs. So, do you just slap some oil in there and hope for the best? Absolutely not! The viscosity, type, method of lubricating, and the quantity are all determined by your particular equipment.
Viscosity
A lubricant’s viscosity is an important property (most experts will say it is the most important) as it ensures the load carrying ability of the lubricant is at its most effective. Viscosity is determined by your equipment’s operating temperature, rotating speed, and load. Oils with a lower viscosity will have higher shear rates than higher viscosity oils. If you use a lower viscosity oil while operating under high temperatures, the oil film will deteriorate and metal-to-metal contact will occur causing wear, corrosion, and damage. If the viscosity is high, but operating temperatures are low, resistance to flow will increase the temperature, cause overheating, breakdown of the oil film, and oxidation of the oil. Consulting your equipment’s OEM manual will help you acquire viscosity recommendations.
Types of Lubricant
The particular type of lubricant used is determined by service temperatures and operating speed. There are two lubricants used – grease and oil. Though most lubricants are petroleum-based, there are synthetic lubricants available. Both are subject to differing degrees of oxidation and deterioration, and are suitable for certain types of components and temperatures. Synthetic oil is less sensitive to fluctuations in temperature and oxidation – making it longer lasting and not needing to be changed as often. Hydrocarbon oil is more widely used, but synthetics are becoming an ever-popular choice for consumers.
Methods of Lubrication
There are different methods of lubricating your rotating equipment:
Oil Misting: Mist generator systems are centralized systems of compressed gas that is used to atomize oil. Low pressure systems then distribute the atomized oil at multiple dispersal areas for optimal lubrication. Oil mist systems are highly effective at keeping equipment lubricated and minimizing temperature fluctuations. This is the best lubricating technology available on the market today.
Grease: The lubricant of choice for most machine elements, but is limited by service temperatures. Grease has additional sealing properties and minimizes leakage and contaminants. Unfortunately, grease lubrication does not dissipate heat like oil mist and oil splash systems. Because it is highly resistant to motion, it takes longer at start-up for adequate lubrication to occur.
Oil Splash: Splash lubrication is the most common method of lubrication. In this method, parts can be in direct contact with the lubricant, or oil rings and flingers may be used. As in the mist generator systems, splash lubrication is effective in regulating temperature. Splash lubrication is at its most effective when oil is filtered and replenished regularly. With oil rings and flingers, parts are not in direct contact. The oil ring or flinger picks up oil and transfers the lubricant over the rotating parts. Oil rings and flingers require close monitoring of lubricant levels — too much oil and the ring or flinger becomes submerged and will not adequately splash the oil; if the level is low, it will not pick up enough oil to lubricate the parts.
Quantity of Lubricant
Too much lubricant and your rotating equipment must work harder to move causing it to overheat; too little lubricant, friction increases, oil film fails, metal-to-metal contact occurs, and your equipment stops operating and needs repairs. Your equipment needs the right amount of lubricant to function at its optimal level.
Keeping your rotating equipment properly lubricated will be one of the most important parts of your maintenance program. Adhering to this will ensure a longer operating life, lower service costs, and reliability of your equipment.
Houston Dynamic Service has over 35 years of experience with rotating equipment service and repair. Give HDS a call to help keep your equipment operating at its peak performance.
Share this post: