Cavitation – One of the Top Six Pump Vibration Problems
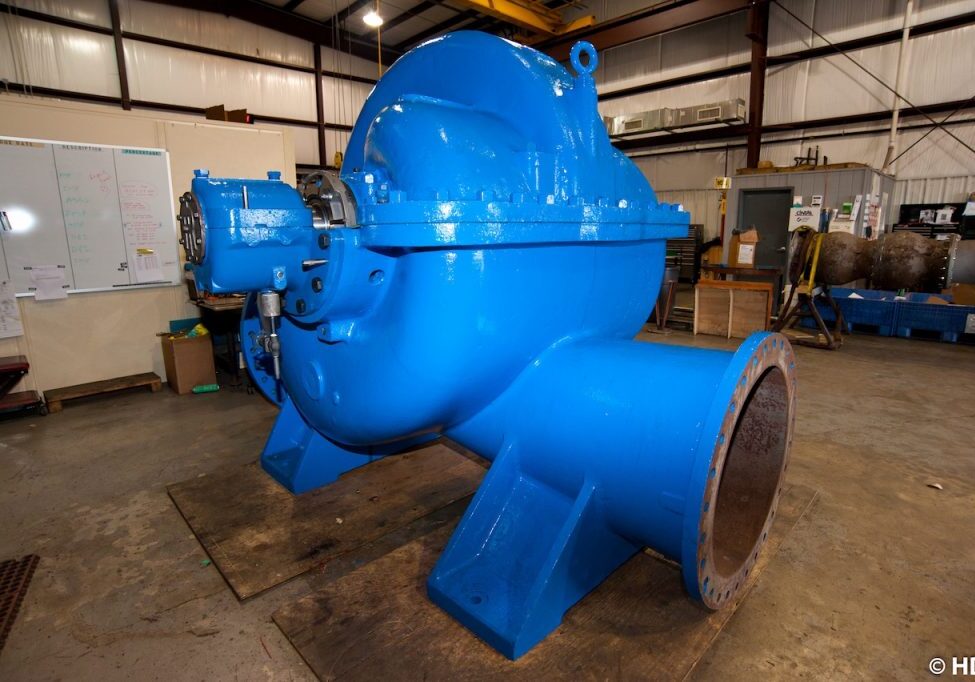
Previously we discussed the top 6 pump vibration problems, with cavitation as the most prevalent. Now it seems appropriate to discuss cavitation further including its causes and prevention methods. In short, pump cavitation is the formation of cavities or bubbles in the pumped media that develop in areas of low pressure around the impeller. When these cavities collapse, they create shockwaves inside the pump that can significantly damage the pump housing or even the impeller.
Pump Cavitation Symptoms
The good news is that many forms of pump cavitation are accompanied by symptoms that are easily detected. They include but are not limited to:
Excess noise such as popping, crunching, rumbling, or the sound of marbles rolling
- Excess energy usage – if the pump is going above and beyond its normal energy use
- Decrease in pump performance – could be a large or small difference
- Impeller that appears to have missing bits – causing a sponge-like appearance
- Inconsistent tank levels
- Changes in the temperature of the pump
- If allowed to continue, the pump may show signs of fatigue on the impeller surface
Types of Pump Cavitation
There are many types of pump cavitation, but the four major ones include:
Suction Cavitation – This type of cavitation is caused when the fluid’s turbulence releases entrained gases into the suction piping. This often occurs when a pump is under low pressure or high vacuum conditions. The pump does not receive enough flow, which allows cavities or bubbles to form at the eye of the impeller. As they carry over to the pump’s discharge side, the bubbles are compressed causing them to implode against the impeller.
Vaporization Cavitation – This occurs when the liquid within the pump vaporizes as the result of a loss of suction head or when the pressure becomes too low or too high. All centrifugal pumps have a required suction pressure operating range to prevent vaporization. However, this requirement is often calculated with the assumption that it operates with fresh water at 68 degrees Fahrenheit. When this is not the case, vaporization can happen.
Vane Passing Syndrome – When the OD of the impeller passes too close to the pump cutwater, it can cause damage. The liquid velocity increases as it flows through the small passage, lowering the pressure and causing vaporization. Bubbles are formed by this collapse just beyond the cutwater. Damage is typically limited to the center of the impeller’s vane and does not extend into the shrouds on a closed impeller.
Discharge Cavitation – If the discharge pressure of a pump is too high or runs at less than 10% of its best efficiency point, it can cause discharge cavitation. The high pressure can keep fluid from flowing out of the pump, instead causing it to circulate in the pump. The resulting vacuum at the housing wall supports the formation of cavities or bubbles, which cause shockwaves when they implode.
How to Prevent Pump Cavitation
There are many ways to prevent and treat pump cavitation, some of which include:
- Evaluate pump design – the path the liquid takes to get to and from a pump should be ideal for operating conditions. When cavitation or other problems arise, rearranging the pump design can resolve the issue.
- Check filters and strainers for clogs as this can cause cavitation.
- Check the pump curve – a pump should run at its best efficiency at the max of the curve. Keep a minimum impeller tip to cutwater clearance of 4% of the impeller diameter for impellers under 14 inches to prevent Vane Passing Syndrome. For impellers greater than 14 inches in diameter, a minimum 6% clearance should be ensured.
- Increase the distance between the actual local static pressure in the fluid and the vapor pressure of the fluid at actual temperature.
If you have a pump that is showing signs of cavitation, contact us. HDS operates a modern repair service center that is strategically located in southeast Houston and is capable of handling all your repair needs.
Share this post: