6 Valuable Tips for Improving Your Equipment’s Reliability
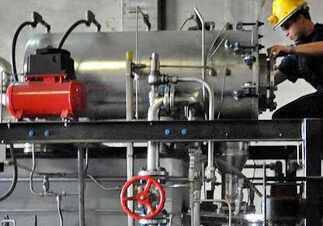
Your critical rotating equipment are some of the most valuable and expensive assets your company owns. Without them, you cannot manufacture great products for your customers, right? So, you probably want to know how to get the most out your equipment, keep it reliable, and running smoothly.
1. Invest in Operator Training
If you train your operators, they will know how the equipment should function, its peak/optimum performance standards, and how to correct issues or problems as they arise. Letting an untrained operator take a whack at your expensive asset is like leaving a toddler in charge of preparing a five-course dinner…it’ll be messy, someone will get hurt, and a lot of things will end up broken. Newbie operators are costly – they shut equipment down for small issues, run up costs because they are constantly contacting maintenance for those small issues, and are always halting production because of the shutdown. Training may cost a little upfront, but it pays for itself when you are not paying for down-time, maintenance, or injuries.
2. Be Conservative With Cross-Training
A view that has been widely held is to cross-train your operators on multiple pieces of equipment; in short, should an employee call out sick or leave, you’re not left in a lurch. The theory is great, the execution, not so much. Cross training on one or two pieces maybe, six or seven, how much can an operator remember? You operators and your equipment should be BFFs, know each other’s favorite colors, and are like family members. Seems silly, but if your operator knows the ins and outs of the equipment they are using, they will more likely know its optimum operating parameters, when to shut it down for maintenance, and how to avoid a major problem.
3. Make Safety a Top Priority
Reliability and safety go hand-in-hand. If you are not adhering to prescribed maintenance schedules, having trained workers operate your equipment, and putting safety first, you are not going to have a dependable machine. If reliability is an issue in your plant, your operators are most likely taking risky shortcuts when it comes to maintenance to keep up production. When your operators take risks, they are playing a dangerous game of Russian roulette with the health and safety of not only themselves, but their co-workers too. Safety doesn’t happen by accident, it is a continuous process that involves every member of the team to do his or her part. If you want a reliable machine, make it safe first.
4. Have Systems in Place That Alert You to Equipment Problems
Your equipment can tell you when it’s operating correctly, when it’s starting to have some problems, and when it needs a break. When you use Statistical Process Control (SPC), you can take the minutest data and adjust your equipment that helps it work more efficiently. It will also help you avoid costly repairs by alerting you to potential problems. Training your operators on SPC analysis is a powerful way of not only empowering your workers, but also nipping issues before they snowball into massive problems that cause injuries or repairs.
Management and operators don’t necessarily see eye to eye when it comes to equipment. Operators believe management does not take their complaints seriously; management thinks the operators doth protest too much. Operators need good statistical backup so management has tangible data to verify and rectify the problem. To drive change, your operators need to take the data they record and put it to good use.
5. Put Checklists in Place
Checklists are an operator’s best friend. They ensure that all procedures for operating a piece of equipment is done in the correct order. Do you think Neil Armstrong, Buzz Aldrin, and Michael Collins skipped performing their checklist on Apollo 11 before blast-off? A great checklist will tell your operators when to start things up, when to perform maintenance, when to shut it down, and when to make changes based on the feedback the operator is receiving. Checklists keep your workers safe and your equipment running.
6. Learn the Art of Clean
If you want an efficient, peak performing piece of machinery, then you need to learn the art of clean. It is no secret that a clean machine operates better and for far longer than its unkempt counterpart. This goes back to training your operators — teaching them how to perform routine operator care. Not only must you teach them, you must give them time during their shifts to do so. It is a guarantee that you will see an increase in productivity and profits and a reduction in maintenance costs.
Improving your equipment’s reliability starts with your operators. By giving them the right tools, you are helping them assist you in protecting your assets and themselves. A well-trained operator will keep your equipment running smoothly and keep you in production.
Share this post: