6 Steps to Optimize Maintenance Practices
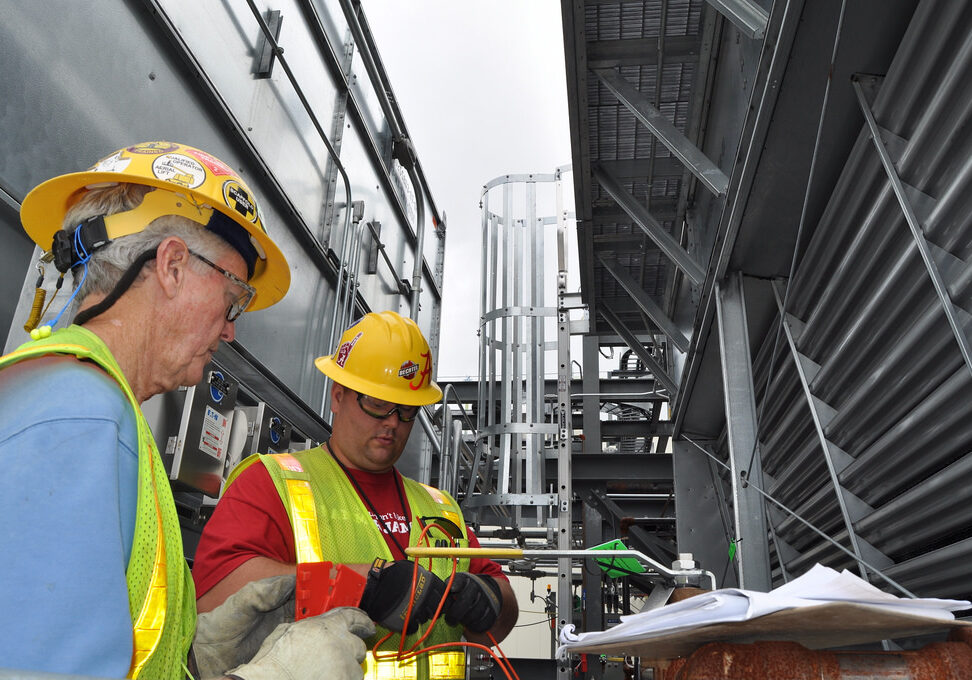
Plant owners across the globe are aware Lean maintenance practices can improve production, minimize downtime, and reduce costs. Unfortunately, as much as 90% of performed maintenance in the United States is done reactively, instead of proactively. Reasons for this include aging equipment, scarcity of spare parts, and the increasingly higher demand in manufacturing speed. We believe it’s possible to save time and money while applying best practices in maintenance. We’ll show you the top 6 steps below.
- Gather as Much Data as Possible
Your organization will need to assemble information to identify the scale of the challenge before successfully transitioning into maintenance best practices. Gather comprehensive data on items such as time between machine failures, machine downtime, cost of parts, technician response time, and even on-time delivery percentage. You can then calculate the average cost of just one hour of downtime.
- Invest in Correct Training
You can only expect expert results from actual experts. In many cases, maintenance can be mostly taught on the job. Your personnel mainly gather their knowledge on your specific equipment and processes by observing and learning from others in the plant. Unfortunately, they may also be learning outdated practices or bad habits. Low-value training results in low-value performance. Your personnel must have the latest and best knowledge in order to be able to contribute to your growth. This can include doing everything from sending them to seminars to hiring experts to speak at your plant.
- Calculate the Cost of Maintenance.
Now that you know what it costs for machine downtime and personnel training, it’s time to determine what it will cost to maintain your equipment. Do this by combining the cost of downtime, cost of spare parts, cost of maintenance materials, cost of maintenance personnel, and any other related expenses. Project reasonable assumptions by applying the cost per-hour of downtime to availability of equipment in order to determine how much an uptake in availability will add. You are likely to find even an increase as small as 5% can convert into an enormous improvement.
- Get the Right Tech
We all know the automation age is upon us. A menial task that was normally done by hand can now be done via machine, freeing up time for your personnel to perform other more important tasks. A technology solution makes it easier to control all sorts of variables. For example, a Computerized Maintenance Monitoring System can deliver work order information while improving response time at a fraction of the cost when calculated over time. A CMMS can also lower the mean time to repair that reduced downtime.
- Create and Deploy a Comprehensive Plan
This includes but is not limited to:
- Schedule preventive maintenance ahead of time.
- Develop a scheduler planning function to optimize your techs’ time, as well as ensure all parts and supplies are available ahead of time.
- Use predictive tools such as vibration analysis, leak detectors, a thermography tool for electrical equipment, etc.
- Bring in Third Party Contractors
Even with all the above, there will still be holes in your maintenance practices. This is why it is so important to find and hire third party contractors who are familiar with your equipment, process, industry, etc. When looking for experts outside your organization to achieve your required results, be sure to get references from past and existing customers to ensure they are the right fit for your organization.
HDS has a fully staffed service center with experienced personnel, dedicated to quality and trained in the most current rotating equipment maintenance, inspection, and repair techniques for your industry. Call us today to discuss your optimized maintenance needs.
Share this post: