3 More Tips for Implementing a Predictive Maintenance Program
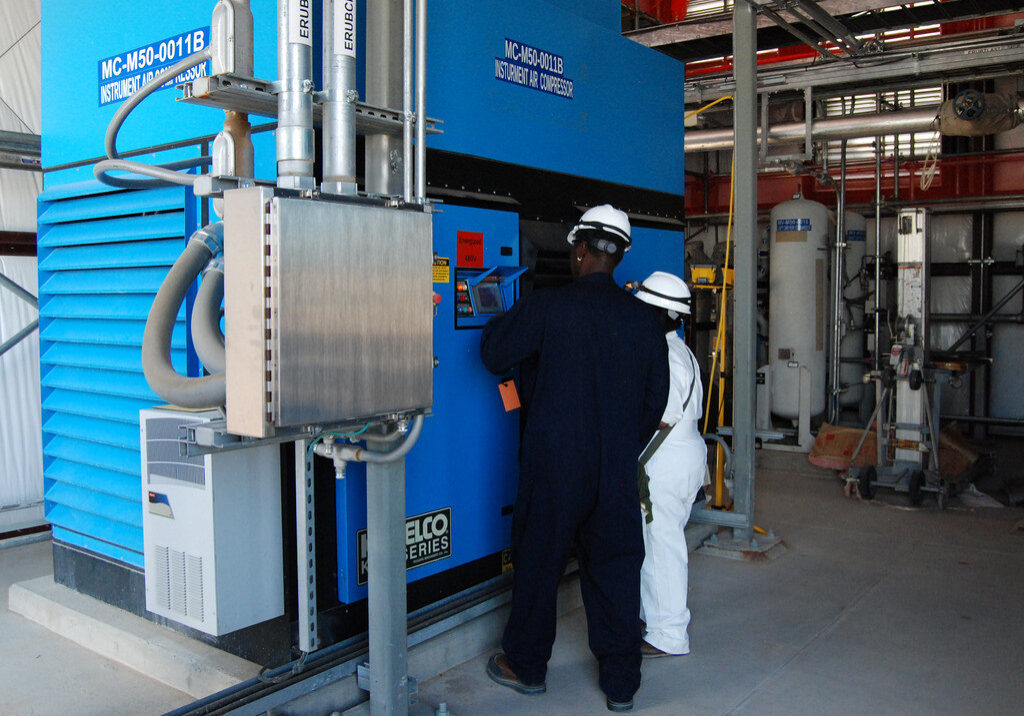
We have previously written about Tips for Implementing a Predictive Maintenance Program and want to go a little deeper. Prioritizing your assets, identifying key performance indicators, and utilizing the best tech are anll great ideas. But we have more below.
-
Focus on Staff Training and Management of Changes
It is essential that all necessary owners, managers, engineers, workers, and even contractors are on board with and understand your predictive maintenance program, as well as its intended goals and each of their roles in achieving them. This often includes developing training programs that include how to implement predictive analytics in their respective areas of responsibility. They must also be shown how to collect the data needed to drive your maintenance practices. This transition will be difficult at all levels, so be sure to adopt practices that allow for staff adjustment, questions, and especially suggestions for improvement.
-
Develop Your Predictive Models
Now that your staff knows what data to collect and why, it is time to use it to develop models to predict everything from maintenance needs to total equipment failure. Utilize advanced analytics which can include sensors, data collection devices, and specialized software to analyze it all and create predictive insights on your specific application or even entire operation. For example, these models can tell that certain rotating equipment tends to slow down after a certain number of hours in operation at certain RPMs and can determine a maintenance plan for those machines. We also encourage implementing a feedback loop in the models that allow you to develop new data and updates when necessary to improve maintenance practices over time.
-
Pilot Test
You may also pilot test on select assets to check on the effectiveness of your predictive maintenance program versus those assets who have not utilized your new initiatives. The practice allows you to A/B (and even C and D) test your performance data. This data is essential for implementing practices on remaining operations, as well as fine tuning your current program. You may then use these findings to expand your new practices into other areas of your facility and even at other locations with a smaller initial setup cost and shorter time to gather critical data.
How HDS Can Help You Continue to Implement a Predictive Maintenance Program
The team at Houston Dynamic Supply can help you initiate and improve upon your predictive maintenance program. We do so by conducting advanced inspections, diagnostic testing, and data gathering on your rotating and other equipment to identify any opportunities for improvement. We can also take the data from your key performance indicators to help develop an improved maintenance plan, as well as perform repairs and rebuilds in our local facility. Contact us to speak with our experts about how we can help.
Share this post: