Top 5 Rotating Equipment Safety Best Practices for Reliability and Maintenance Management
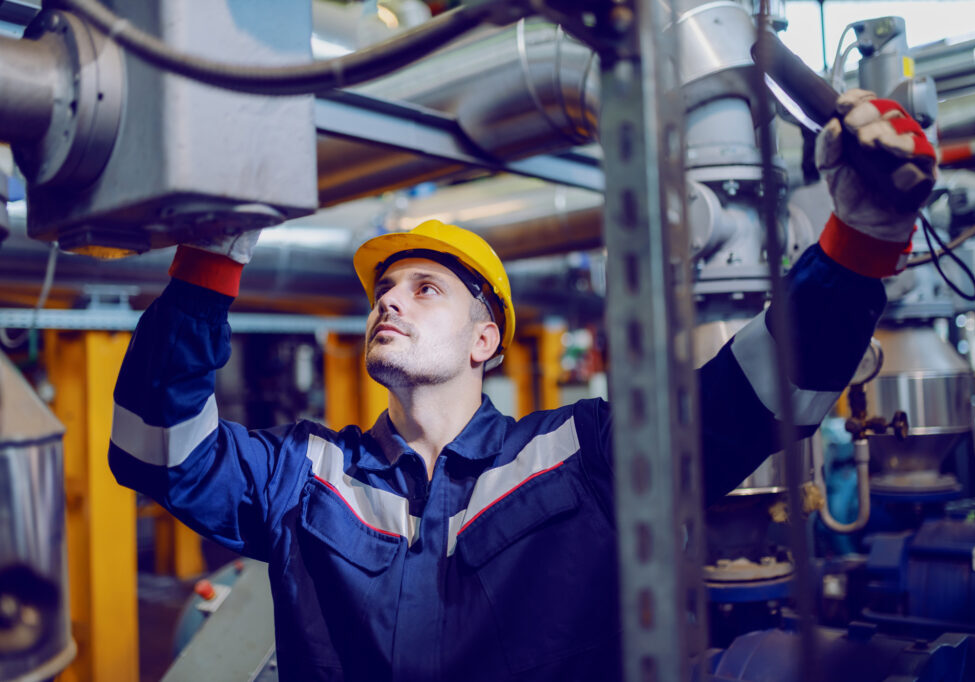
Rotating equipment plays a fundamental role in industrial operations, powering everything from pumps and compressors to turbines and conveyors. However, with its critical function comes significant safety risks. The U.S. Bureau of Labor Statistics (BLS) reports that machinery-related accidents account for nearly 15% of all workplace fatalities in manufacturing and industrial settings. The key to minimizing these risks lies in proactive maintenance, proper machine safeguarding, and strict adherence to safety standards.
Following are the top five rotating equipment safety best practices—designed not only to protect employees from injury but also to enhance equipment reliability, reduce downtime, and improve operational efficiency.
1. Prioritize Preventive and Predictive Maintenance
Poorly maintained rotating equipment poses the highest risk to both personnel and operational integrity. Unlubricated bearings, misaligned shafts, and excessive vibrations are all common issues that, if left unaddressed, can lead to catastrophic failures. According to the Occupational Safety and Health Administration (OSHA), nearly 30% of machine-related injuries result from mechanical failures—most of which are preventable with proper maintenance.
Key Maintenance Strategies for Safe Operations:
- Lubrication Management: Use condition-based monitoring (CBM) to assess lubricant quality and contamination levels. Inadequate lubrication can cause overheating and increased friction, leading to premature failure.
- Vibration Analysis: Employ predictive maintenance tools like vibration analysis and ultrasonic testing to detect misalignment, imbalance, or bearing defects before they cause critical damage.
- Torque and Fastener Inspections: Loose bolts on rotating machinery can lead to unintended part ejection, causing serious injuries and damage to adjacent equipment. Regular torque inspections help mitigate this risk.
- Alignment and Balancing: Improper shaft alignment increases wear on bearings, couplings, and seals. Using laser alignment technology can help ensure precision.
- Thermal Imaging: Excessive heat generation in motors and gearboxes often indicates an impending failure. Infrared thermography can detect hot spots before they become hazards.
By implementing a robust maintenance strategy, companies can reduce unexpected breakdowns by up to 60% while significantly enhancing workplace safety.
2. Implement a Comprehensive Machine Safeguarding Program
Machine safeguarding encompasses the standards, tools, and procedures that protect workers from hazardous contact with rotating machinery. Studies indicate that a lack of proper safeguards contributes to nearly 50% of all rotating equipment injuries.
Essential Safeguarding Strategies:
- Hazard Identification: Conduct thorough risk assessments to determine which parts of the equipment require safeguarding. Common danger zones include pinch points, shear points, and nip points where moving parts interact.
- Engineering Controls: Whenever possible, use fixed barriers, interlocked guards, and automatic shut-off features to eliminate direct contact with rotating components.
- Administrative Controls: Train employees on safe work practices, hazard recognition, and emergency response procedures. A well-informed workforce significantly reduces the likelihood of accidents.
- Standard Operating Procedures (SOPs): Develop detailed SOPs outlining safety measures for equipment operation, maintenance, and lockout/tagout (LOTO) procedures.
OSHA recommends safeguarding strategies such as elimination, substitution, and engineering controls to minimize workplace injuries. Integrating these practices into daily operations is crucial for compliance and risk mitigation.
3. Utilize Proper Guarding for Rotating Equipment
Unprotected rotating machinery poses a severe threat, with OSHA regulations (29 CFR 1910.212) requiring safeguarding for:
- Points of Operation: The area where work is performed, including cutting, shaping, or drilling zones.
- Power Transmission Components: Shafts, belts, pulleys, gears, couplings, and flywheels that transfer motion.
- Exposed Moving Parts: Any reciprocating, meshing, or rotating component that could entangle an operator.
Recommended Guarding Solutions:
- Fixed Guards: Permanently attached barriers that cover hazardous areas, preventing access to dangerous components.
- Adjustable Guards: These offer flexibility for varying tasks while still ensuring protection from rotating parts.
- Interlocked Guards: Automatically shut down machinery when removed, preventing accidental exposure to moving parts.
- Enclosures and Shields: Used for high-speed rotating equipment, such as turbines, to prevent debris ejection in case of component failure.
Proper guarding not only protects employees but also enhances equipment longevity by preventing debris ingress and contamination, which can lead to premature wear.
4. Implement Advanced Safety Devices for Access Control
While guarding is the first line of defense, additional safeguarding devices provide an extra layer of protection by restricting access to dangerous machinery. Advanced presence-sensing and emergency stop mechanisms can drastically reduce workplace injuries.
Top Access Control Solutions:
- Two-Hand Controls & Trips: Operators must engage both hands to activate the machine,
- ensuring their hands are kept away from danger zones.
- Pullbacks & Restraints: These use cables or straps to physically prevent operators from reaching hazardous areas.
- Safety Trip Controls: Includes tripwires, trip rods, and body bars that immediately stop the machine when contact is detected.
- Moveable Barriers: Ensures workers are physically separated from rotating equipment during operation.
- Presence-Sensing Devices: Light curtains, laser scanners, and pressure-sensitive mats detect when a body part is too close to the danger zone, stopping machine operation.
According to OSHA, the use of advanced safeguarding devices can reduce machine-related injuries by up to 70% when properly integrated into a safety management system.
5. Enforce Proper Personal Protective Equipment (PPE) and Attire
One of the most overlooked yet preventable causes of rotating equipment injuries is improper attire and loose-fitting clothing. The National Safety Council (NSC) reports that entanglement in rotating machinery accounts for 20% of all severe workplace injuries.
Essential Attire and PPE Guidelines:
- Wear Close-Fitting Clothing: Loose shirts, long sleeves, and untucked clothing can get caught in moving parts.
- Secure Long Hair & Beards: Employees should tie back or fully cover long hair to prevent entanglement.
- Avoid Jewelry: Rings, necklaces, and bracelets can become snagged in rotating components, leading to severe injuries.
- Glove Use Precautions: Unless required for chemical or thermal protection, avoid gloves around rotating shafts and moving parts to prevent accidental entanglement.
Strict adherence to these guidelines prevents life-threatening injuries, such as severed fingers, crushed limbs, and scalping incidents—all of which are documented risks in industrial environments.
A Safer, More Reliable Work Environment
Implementing these five key rotating equipment safety practices not only protects employees but also enhances equipment reliability, minimizes unplanned downtime, and reduces costly worker’s compensation claims. Companies that prioritize proactive maintenance, safeguarding strategies, and strict safety protocols experience up to 40% fewer machine-related incidents and a substantial improvement in operational efficiency.
By fostering a culture of safety and reliability, industrial facilities can ensure compliance, protect their workforce, and maximize the lifespan of their critical rotating equipment. Prioritize safety today to prevent accidents tomorrow.
With over 50 years of experience, Houston Dynamic Services is dedicated to providing top-tier rotating equipment repair and upgrade solutions. Our skilled team ensures your machinery operates at peak performance, minimizing downtime and maximizing efficiency. Trust us to be your reliable partner in maintaining and enhancing your critical equipment.
Share this post: