Main Pump Types – Rotary
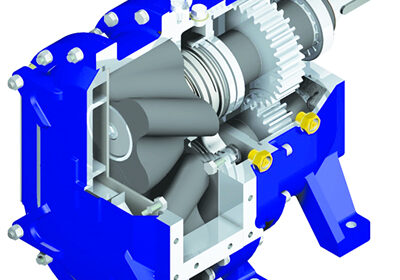
Continuing with our series on the main types of pumps, next in line is the second type of positive displacement pumps, which are rotary pumps. Both types of positive displacement pumps, reciprocating pumps and rotary, can be further divided into categories of commercial applications, and it is important to know what they are as well as how they work.
Rotary Pump Basics
Rotary pumps operate with the use of a rotor or turning mechanism. They often include grates or vanes. Each mechanism works in a different manner and can even feature the rotor on the inside or outside of the pump.
Types of Rotary Pumps
The two major types of rotary pumps are those with single or multiple rotors.
Single Rotor Rotary Pumps
- Flexible member – Flexing vanes are used to move media. Pumping and sealing is dependent on the elasticity of these flexible vanes. They can also be a tube or liner.
- Peristaltic – A flexible tube inside a circular casing is usually used, although there are linear peristaltic pumps. The rotor turns these tubes to open it move fluid through. After the passing of the cam (restitution) the tube opens to its natural state. Tubes can be rollers, wipers, or shoes.
- Piston – These are usually multiple rotor pumps but can be single.
- Screw – A screw or screws are turned to move media. Fluid is displaced axially as screws mesh. Also called progressive cavity pumps, screw pumps use a stator with internal threads and a rotor with external.
- Vane – Vanes work with a cam to draw media into and out of the pumping chamber. Vanes may include buckets, blades, slippers, or rollers. These components may be located in the rotor or in the stator. Vane rotary pumps can have constant or varying displacement pump elements.
Multiple Rotor Rotary Pumps
- Circumferential piston – Rotating pistons are used to move fluid and rotors are timed separately. More than one rotor is often used with one or more pistons.
- Gear – Whether internal or external, turning gears are used to move media. They spin in order to move media from the inlet to the outlet ports. An outer gear can drive the inner or idler gear on a stationary pin. Pumping action creates voids as they are released from mesh, then liquid flows in. Gears rotate back into the mesh, reducing volume, and forcing liquid through the discharge port.
- Lobe – Two or more lobes, or devices that look like fidget spinners, are used to move media. It is driven between the rotor teeth and chamber with the surface creating continuous sealing. Rotors may be bi-wing, tri-lobe, or multi-lobe.
- Screw – A screw or screws are turned to move media. Fluid is displaced axially as screws mesh. Also called progressive cavity pumps, screw pumps use a stator with internal threads and a rotor with external.
Applications for Rotary Pumps
Rotary pumps operate with the use of high pressure in many applications. They are beneficial due to their small size and can be used for anything from disposing of waste to pumping gas. Rotary pumps deliver continuous flow at high differential pressure. The pumps are also self-priming and offer a consistent flow, even when pressure varies.
When compared to centrifugal pumps, rotary pumps can handle far more viscosity, up to 1.32 million cSt or 6 million SSU. However, they have a lowered max capacity. Rotary pumps offer excellent efficiency, flow control, and help reduce energy costs at higher levels than centrifugal.
Conclusion on Rotary Pumps
At Houston Dynamic Service, we have extensive knowledge on a wide range of pumps and applications. We provide expert maintenance and repair for rotary pumps and many others. To learn more, contact us to discuss how we can keep your pumps running efficiently with less down-time.
Share this post: